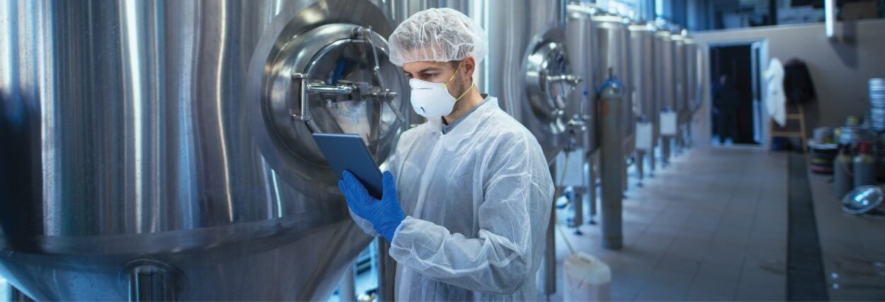
When it comes to protecting your workers, it's crucial to follow recommended guidelines and safety precautions. If your employees don't have the right personal protective equipment (PPE) for the job, their health and safety are at risk, which is potentially a huge liability.
To make it easier for employers and job sites to stay safe, the Environmental Protection Agency (EPA) and Occupational Health and Safety Administration (OSHA) have strict rules regarding PPE types necessary for dangerous situations.
Before sending your workers into a hazard zone, you must be prepared. So, what are the EPA levels of protection? This article will break them down in detail, complete with examples of when they may be necessary.
What are the EPA Protection Levels?
There are four distinct categories outlined by the EPA and enforced by OSHA. In each section, we'll outline the specific protocols necessary for each level and the required PPE. Here is what you need to know.
Level A Protection
This level is the most severe, meaning that the situation poses the highest risk to workers. For an environment to be at Level A, there must be an elevated risk of damage to the skin, eyes, and respiratory system. This damage can come from chemical, biological, or radioactive elements. So, individuals must be covered from head to toe with sufficient PPE to protect all parts of their body.
Although fires can be dangerous enough to warrant a Level A rating, there are unique regulations regarding protecting workers in case of fire hazards. In those instances, clothing must be flame-resistant, and multiple layers of clothes might be required.
PPE Necessary for Level A Situations
From the inside out, employees will require:
- Disposable Protective Suit, Gloves, and Boots
- Inner and Outer Chemical-Resistant Gloves (Different From the Ones Above)
- Fully Encapsulated Vapor and Chemical-Protective Suit
- Positive Pressure, Full-Face Self-Contained Breathing Apparatus (SCBA) With Air Respirator
As you can see, individuals must wear multiple protection layers to ensure that a breach in one of the outer suits won't create an unsafe situation. For a suit to be rated as chemical and vapor-protective, it must pass various spill and air-tightness tests. A perfect example of this kind of PPE is a certified HAZMAT suit.
Examples of Level A Situations
Since Level A events are the most dangerous, they are also less likely to occur. However, here are some prime examples of Level A situations:
- Toxic Waste Spill
- Chemical Spill
- Radiation Spill
Level B Protection
Next, at Level B, the primary concerns are vapors or other airborne toxins that can damage the respiratory system. As long as these toxins are not corrosive or damaging to the skin, Level A is not required. That said, the hazards are similar enough that workers will need much of the same PPE as Level A. However, instead of a full-body protective suit, individuals can stay safe with coveralls and hooded chemical-resistant clothing.
PPE Necessary for Level B Situations
- Coveralls
- Hooded Chemical-Resistant Clothing
- Inner and Outer Chemical-Resistant Gloves
- Face Shield
- Outer Chemical-Resistant Boots
- SCBA Gear With Air Respirator
Examples of Level B Situations
- Airborne Viral Outbreak
- Toxic Gas Leak
Level C Protection
As we move down the list, each situation calls less for skin protection and focuses more on keeping the lungs safe and healthy. For Level C events, the presence of toxic vapors or gases in the air is low enough to allow for personal air purifiers, rather than a full SCBA setup. Before sending workers into the field, teams will conduct tests to ensure that airborne toxicity is manageable.
PPE Necessary for Level C Situations
- Full-Face Air Purifying Respirator
- Escape Mask (Portable Respirator)
- Hard Hat
- Inner and Outer Chemical-Resistant Gloves
- Disposable Chemical-Resistant Outer Boots
Workers do not need chemical-resistant clothing or a full-body suit to protect themselves. However, having a backup escape mask is vital in the event that the original respirator malfunctions or the purifying filter needs changing.
Examples of Level C Situations
- Airborne Disease Outbreak (Low Contagiousness)
- Light Chemical Spill
- Construction Sites with Heavy Dust or Vapors
Level D Protection
The lowest risk category, Level D, can be utilized for everyday workplaces. That said, there may be potential for splashes or unexpected hazards, so workers still need basic protection. However, suppose these hazards could significantly damage the eyes, skin, or respiratory system. In that case, Level D will not be sufficient, no matter how many other precautions are in place.
PPE Necessary for Level D Situations
- Coveralls
- Face Shield
- Gloves
- Safety Glasses
- Chemical-Resistant Steel-Toe Boots (or Shoes)
At first, it may seem odd that Level D requires coveralls, but Level C does not. The reason for the disparity is that Level D sites can have both airborne and physical hazards, such as chemical splashes and fumes, or heavy equipment. As such, the PPE standards must accommodate a wider variety of situations and potential threats.
Examples of Level D Situations
- Construction Sites
- Chemical Cleanup with No Airborne Vapors Present
What is An Employer's Responsibility When Supplying PPE for Hazardous Situations?
While the EPA is in charge of setting and updating these hazard level guidelines, OSHA is responsible for enforcing them on job sites around the country. There are two employer requirements, as outlined below:
Hazard Assessment and Prevention
The best way to keep workers safe is to prevent dangerous situations from developing. For example, if your employees work with hazardous chemicals, you may have multiple redundancies in place to ensure that none of the liquids spill. These measures can include proper safety training, secure transportation containers, and protocols for handling and moving each unit.
Workplaces are also responsible for conducting regular on-site inspections of all safety practices to make sure that employees are following them correctly.
PPE Management
Employers are ultimately responsible for all PPE used by workers on the job. Even if an employee brings personal equipment, the employer must inspect it to ensure that it follows all EPA and OSHA regulations. For example, if a worker brings non-chemical-resistant boots, the employer must provide replacements or send them home.
PPE stock must also be managed with equipment getting replaced and inspected regularly. There should be a system in place for workers to notify supervisors of any upcoming shortages so that the materials can be restocked before running out.
If a workplace is using reusable PPE, the employer is responsible for maintaining the equipment to adhere to EPA and OSHA standards. If any PPE is damaged or does not function correctly, it must be discarded and replaced immediately.
Finally, employers must provide training for all PPE used on the job. This training may be necessary even for equipment that is relatively self-explanatory (i.e., coveralls). Part of the reason for training is to show workers how to use the PPE and how to remove and dispose of it as necessary. For example, if an employee touches corrosive chemicals with their gloves, they need to know how to remove the gloves without touching any skin, where to dispose of them, and how to properly dispose them to prevent skin contact with others.
What Happens If an Employer Doesn't Follow These Rules?
There are several ways that employers could face consequences for failing to provide sufficient health and safety standards in the workplace.
- First, employees are legally allowed to file a whistleblower complaint without fear of retaliation.
- Second, OSHA may issue citations and steep fines.
- Finally, OSHA can force a company to halt operations until its job site is up to code.
Disposable PPE Designed with Wearer Feedback
Knowing the OSHA/EPA protection levels is one thing; providing effective PPE for your employees is another. Rather than conducting in-house tests to ensure that all your equipment follows EPA and OSHA guidelines, you can work with a well-respected company that only sells high-grade, disposable materials.
International Enviroguard is committed to providing the best PPE across a wide array of industries. From bloodborne pathogens to flames and chemicals—and everything in between—we have disposable, protective workwear needed to keep workers safe. All our products are rigorously tested to ensure safety, compliance, and comfort.
View all our disposable, protective clothing, browse by industry, or browse by protection type needed.