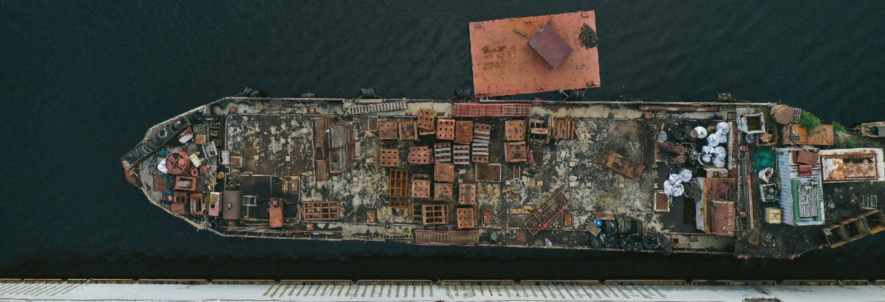
More than 7,000 vessels have been beached in Asia since 2009 for recycling purposes, and ship breaking safety standards have been almost non-existent. Reports indicate that thousands of people involved in the ship breaking process have lost their lives to workplace accidents, and an untold number likely perished from exposure to hazardous materials and airborne particles infiltrating their lungs.
It’s no coincidence that upwards of 90 percent of ship recycling tonnage occurs on beaches in Bangladesh, India, Pakistan, and China, in areas where workers are significantly underpaid and have little access to health risk information. Big corporations appear to be putting their bottom lines ahead of human beings. However, heightened awareness of the poor working conditions and lack of personal protective clothing and equipment for workers continues to grow.
Unless ship breaking safety standards improve dramatically, companies can anticipate heavy fines and class action lawsuits that will likely force them into bankruptcy. The time is now to do the right thing and provide adequate protective clothing for ship breaking yard workers.
What is Ship Breaking?
Commonly given the environmentally friendly moniker — “Ship Recycling” — ship breaking involves the complete dismantling of a vessel for profit. The ship breaking process consists in taking vessels that have exceeded their usefulness and stripping them of machinery, equipment, and materials that can be sold for repurposing or recycling.
Much of the steel removed from retired vessels can be melted down and used to manufacture new products. This recycling aspect typically saves companies money while also reducing mining and smelting processes. Other materials such as wood, glass, aluminum, and cast iron, among others, are widely reused as well. Ship breaking provides a necessary function for vessels that are no longer seaworthy. However, many of these operations put workers at heightened risk of injury, illness, disease, and death.
The working conditions and inherent hazards associated with ship breaking have drawn media attention in recent years. Outside Bangladesh, The Guardian reported that upwards of 25,000 people work 12- to 16-hour shifts, seven days a week. The workplace and surrounding coastal environment are rife with ship breaking hazards, including flammable oil, hazardous chemicals, and asbestos. In 2019, 26 people died from ship breaking injuries, and more than 200 fatalities occurred at the Bangladesh-based ship breaking shoreline during a 15-year span. The loss of life due to long-term exposure to hazardous materials and related illnesses has yet to be counted.
What are Common Ship Breaking Hazards?
Considered one of the most physically dangerous jobs in the world, ship breaking safety risks such as exposure to chemical agents and hazardous dust are infrequently addressed. Crew members dismantle massive vessels weighing tons under changing coastal weather and harsh weather conditions.
Despite a growing knowledge that people continue to be exposed to unknown health hazards, protective clothing for ship breaking yard duties is sorely lacking. Rather than outfit hundreds of employees with necessary PPE for shipyard work, corporations put profit over human health, safety, and lives. Consider the fact that few workers are provided PPE during the ship breaking process while conducting the following hazardous activities.
- Scraping and dismantling efforts in confined and enclosed spaces with poor ventilation.
- Working in dangerous atmospheres that include airborne dust particles, mold, asbestos, and more.
- Conducting paint removal, often lead-based paint in older vessels, without proper PPE.
- Cutting metal with power tools and torches.
- Removing oil and fuel from vessels.
- Entering and cleaning fuel holding tanks.
- Performing tasks at heights without ship breaking safety equipment such as harnesses.
- Dismantling and removing ship machinery.
What’s particularly disheartening about the ship breaking industry is that little, if any, efforts are made to formally educate workers about the risks they encounter. Operations often do not have a well-defined fire protection strategy, rescue protocols, or policies regarding ventilation, dangerous chemicals, and exposure to hazardous materials known to cause debilitating illnesses. People who sign on to handle hazardous duties are typically unaware that PPE for shipyard work should be available to every crew member. That’s largely because it remains non-existent at job sites. Companies too often willfully disregard worker health and safety, so they can make more money.
What are the Health and Safety Risks Associated with Ship Breaking?
Perhaps the greatest ship breaking safety risk stems from the fact workers are not provided adequate personal protective clothing and equipment. It’s not uncommon for a demolition crew member to hover within two feet of oxy-acetylene torches burning through hulls, decks, and equipment as hazardous vapors are inhaled and molten metal splatters about. Other routine tasks require unskilled workers to grind and scrape lead paint from old ships. The following rank among the more dangerous ship breaking safety risks.
- Asbestos Exposure: Linked to deadly cancers, this hazardous material is usually found in ship hanger liners, insulation, adhesives, and the gaskets used in piping connections. Dismantling an older ship generally results in workers suffering asbestos exposure.
- Mercury Exposure: Decommissioned vessels that carry toxic materials such as mercury are not managed with increased ship breaking safety standards. Reports indicate that upwards of 1,500 tons of mercury-contaminated material was dumped at a single ship breaking site. Workers routinely face mercury hazards without the necessary PPE for shipyard work.
- Polychlorinated Biphenyls (PCBs): These agents were banned in the U.S. in 1979 because they pose a clear and present public health danger. Upwards of 1.5 billion pounds of PCBs were used in electrical insulators, oils, paint, and capacitors, among others. These hazardous chemicals are still found in old ships that are being recycled.
- Lead: Exposure to lead can result in anemia, kidney failure, and brain dysfunction. This hazardous material persists in ship ballasts, generators, motor parts, and old paint.
- Confined Areas: Working in confined spaces poses a significant health and safety danger across sectors. In the ship breaking industry, workers are often tasked with cutting, grinding, and removing equipment. The heat, airborne particles, and deficient fresh air circulation represent both an imminent safety threat and long-term health risk. These factors can lead to inhalation of toxic vapors, particulates, and unsafe oxygen levels.
Contaminated air and working conditions are only exacerbated by noise levels that damage hearing. So-called “recycling” organizations can no longer hide behind the eco-friendly branding now that wide-reaching media outlets, health organizations, and government officials have learned the truth. Large corporations dump hazardous materials directly into the environment while failing to supply even the most basic PPE for shipyard work.
Beyond the staggering death toll of 2 deaths per 1,000 workers that far exceed mining fatalities (0.34 per 1,000 workers), ship breaking crew members are generally kept in the dark about long-term health effects in this line of work. Some of the illnesses and conditions from inhaling items such as asbestos can take upwards of 15 years to present symptoms.
Ship breaking stakeholders may have believed they were unlikely to be held accountable for debilitating health conditions and loss of life that follows. That’s largely because efforts by the International Maritime Organization to establish minimum ship breaking standards fell short following its 2009 Hong Kong Convention. The proposed health and safety regulations never gained enforcement. However, increased awareness of unsafe working conditions led agencies such as the U.S. Occupational Safety and Health Administration (OSHA) to craft enforceable ship breaking regulations.
What Hazardous Activities are Performed Throughout Ship Breaking?
OSHA’s “Safe Work Practices for Ship Breaking” report provides step-by-step guidance on how to safely perform certain ship breaking tasks. The report highlights many of the inherent dangers involved in the necessary end-of-life recycling process. The following OSHA recommendations provide a roadmap to improved ship breaking safety.
- Conduct a Vessel Survey: After the ship has been beached and the surrounding area dredged, a diagram of the vessel should be created. The diagram should indicate where fuels, tanks, storage compartments, and places that could potentially hold hazardous materials such as asbestos, lead, and PCBs, are located. Advanced teams are tasked with investigating and taking samples to define risks and determine appropriate personal protective clothing and equipment for the shipyard work.
- Hazardous Liquids Removal: Fuel, mercury, and hazardous waste, among others, task supervisors with ensuring diligent safety protocols are followed. These typically involve testing bilge water and having emergency crews and equipment on standby.
- Equipment Removal: A great deal of parts and equipment call for laborers to move heavy or sharp items manually. Proper back supports and PPE to prevent contact with unknown substances are generally advisable.
- Hazardous Material Removal: Due to the heightened risk asbestos and PCBs present, OSHA advises a two-stage removal process. Cutting and hauling away PCB-infested portions of the ship is generally advisable before undertaking tedious asbestos removal. These, and other hazardous elements, require workers to wear personal protective equipment and clothing that meets industry safety standards.
- Surface Preparation: Before sections of the hull or decks can be cut or blow-torched, it’s crucial that toxic coatings be addressed. Older paints often possess ingredients such as lead, asbestos, and heavy metals that can damage the lungs. Such coatings must be assessed, and any health and safety threats neutralized.
After materials have been safely stripped away from the vessel, it’s critical to thoroughly test for the presence of toxic elements. Although ship parts may be heading to a facility that recycles or repurpose them, health and environmental dangers persist.
OSHA Standards: Personal Protective Clothing for Ship Breaking Yard Safety
As a leading organization in worker health and safety protections, OSHA requires ship breaking corporations have the protective equipment and clothing necessary. The federal agency assessed the working conditions, inherent dangers, and tasks involved in the ship breaking process. Its findings led to the following recommendations related to standard protective clothing for ship breaking yard personnel.
- Hard Hats and Appropriate Head Protections
- Goggles and Face Shields
- Protective Footwear and Coverings
- Noise Reduction PPE to Protect Against Hearing Loss
- Respirators and Breathable Masks
- Respirators and Breathable Masks
Ship breaking corporations have earned a reputation for putting profits over people. But as an increased number of worker safety advocates and government officials assess the human cost, a reckoning may be approaching.
Class action lawsuits have defeated seemingly powerful industries such as Big Pharma and Big Tobacco. Ship breaking organizations can anticipate legal action unless they make a concerted effort to provide workers with a readily-available stockpile of protective clothing.