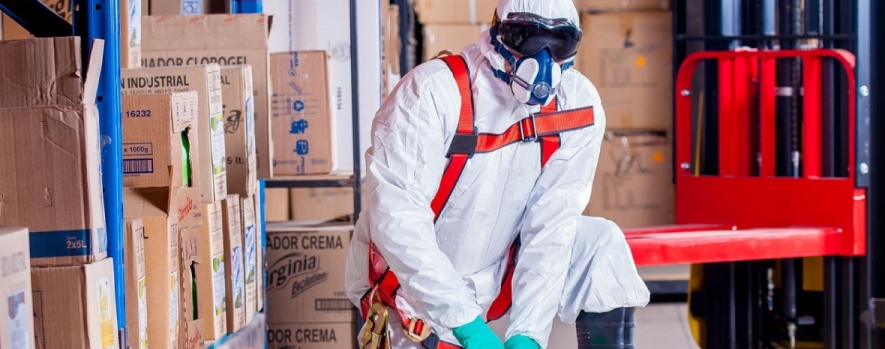
It is the responsibility of OSHA to enforce workplace safety and health laws that protect workers from hazards. Disposable protective clothing is so important that OSHA performs regular workplace inspections. OSHA will cite and/or fine any private industry employer for noncompliance on a per-employee basis.
When workers must perform hazardous activities, the employer must supply the right disposable PPE for them to use. Workers should also be trained in how to use safety equipment and how to put on reusable or disposable protective clothing.
OSHA knows it is impossible to eliminate all hazards that can cause injury or illness in the workplace. Therefore, standards have been set for employers to follow which can minimize worker's exposure to hazards. Part of these requirements will include the use of disposable protective clothing and equipment. Workplace PPE includes:
- gloves
- foot protection
- eye goggles
- coveralls or chemical suits
- ear plugs
- hard hats
- respirators (for any activity where a possible hazard exists)
Workers that are under 18 years old are not allowed to work in hazardous locations. Yet every year, young workers are hurt on the job from performing normal work duties that could be avoided with the right disposable protective clothing.
"Every year 30-50 teens under 18 die from work injuries in the United States. Another 27,000 get hurt badly enough that they go to a hospital emergency room. The most commonly cited workplace accidents for minors include injury by sharp knives, deep fat fryers, slippery floors, and heavy objects."
Every employer must provide personal protective equipment (PPE) for its workers to use for their protection against health hazards, physical hazards, environmental hazards, and hazardous materials.
The Importance of Disposable Protective Clothing
The primary goal of OSHA regulations is to prevent workplace injuries and illnesses. OSHA goes the extra mile to explain exactly what protective equipment is needed, who needs to wear it, and how it is to be worn. OSHA works to help employers stay in compliance with workplace laws and regulations. Disposable protective clothing for employees are also important for other reasons that can directly benefit the employer:
- A reduction in workplace injuries will reduce the cost of workers' compensation premiums
- When workers feel protected, they are more engaged and more productive at work
- A safe workplace can enhance corporate and community social responsibility goals
- Workplace safety guidelines can support daily operations by setting a standard workflow
Supplying workers with personal protective clothing and equipment is a proactive approach to managing the safety and health of employees. Reacting to worker injuries and fearing unannounced OSHA inspections must be avoided. It is better to keep you company in compliance by understanding how disposable protective clothing can help both your business and your workers.
When and Where Disposable Protective Clothing is Needed
Bacteria and Infection Control
When workers are exposed to viruses, bacteria, or any pathogen that can cause illness, they may be required to wear PPE. Infectious bacteria can enter the worker by skin contact, ingested by mouth, inhaled through the nose, or vapors that can affect the eyes and other mucous membranes. The fabric used to manufacture the disposable PPE for testing laboratories and health care facilities should also be able to block transmission of contaminants from blood, body fluids, or respiratory secretions.
Partner with a manufacturer like International Enviroguard that takes extensive input from medical professionals to design disposable protective apparel with a better fit and performance. These garments work to protect healthcare workers against hazardous materials in real-world infectious disease scenarios. Protective lab coats and coveralls should be manufactured from an impermeable fabric with seams that pass ASTM 1670 and ASTM 1671 guidelines for blood and bloodborne pathogens.
Personal protective equipment (PPE) used for health care purposes, are deemed a medical device and must follow FDA's regulations. This includes equipment such as surgical masks and N95 respirators, and some clothing such as medical gowns and gloves.
Hazardous Materials and Chemicals
Clean and undamaged protective gloves, coveralls, and eyewear should be used by any employee that handles a cleaning product that is labeled as a skin or respiratory irritant. It the chemicals that are a part of industrial processes that pose the greater threat to workers.
In these cases, your company's safety program must provide the proper level and type of protection to meet the specific chemicals and concentration levels. Chemical exposure can occur from chemical drips, light chemical splash, and strong jet sprays under pressure.
Refer to the disposable chemical suit manufacturer's product data for information such as:
- European CE Marking - will indicate a chemical suit’s ability to protect against specific hazards
- OSHA Level of Protection 1-4- divides personal protective equipment into four categories based on the degree of protection afforded
- ASTM Approval - determines through testing the ability of a chemical suit ensemble to transfer liquids or vapors
Environmental Hazards
Many workers will face hazards in the environment as a normal part of daily operations. These include:
- Dust, airborne fibers, or irritating gases
- Heat stress or extreme cold
- Human waste or unsanitary conditions
- Loud noise or bright lights
- Repetitive motions
- Confined spaces
- Energized circuits
These environmental hazards may simply be a nuisance, or they could pose a danger to workers when they work in these conditions all day. In these cases, workplace safety training on a regular basis can teach employees when they should wear disposable protective clothing or other PPE to minimize the risk of long-term physical or mental damage.
Management must look for these hazards and determine who might be harmed and how it could happen. Control measures can be put in place to limit or eliminate exposure. Some examples of a control measure include emergency eye wash stations, easy access to ear plugs, disposable safety gloves and disposable uniforms bins, and a clearly defined process for employees to report a safety concern.
Heavy Machinery Operations
Construction sites, factory workers, food and beverage processing, waste water and recycling plants all put workers in contact with heavy-duty equipment that can put workers in direct harm. At other times, worker may be performing duties at heights, near electrical hazards, on slippery surfaces, or near falling objects. Equipment operators may be exposed to hot surfaces, explosions, or caught-in injuries.
The only way to protect employees around heavy machinery is to take a risk assessment of all potential hazards during normal work operations.
Workers can then be protected with uniforms, steel-toed boots, safety glasses and gloves if needed. Don't underestimate the benefit of workplace uniforms. They can eliminate one of the most common accidents involving industrial machine operations - caught in or struck by moving parts of the equipment.
The correct fit of protective clothing in the workplace can help reduce injuries with dangerous equipment. Long shirt sleeves, loose pants, and other outerwear such as jewelry and even long hair can be caught in machines or on sharp edges. Workplace uniforms with cuffed sleeves and fitted ankles allow for the proper amount of body coverage to provide skin protection without the risk of excess fabric that can entangle with moving machinery.
For all these workplace PPE clothing needs, contact International Enviroguard for a full range of protective clothing for workers including disposable protective clothing that is both comfortable and will safeguard your people, productivity and operations.