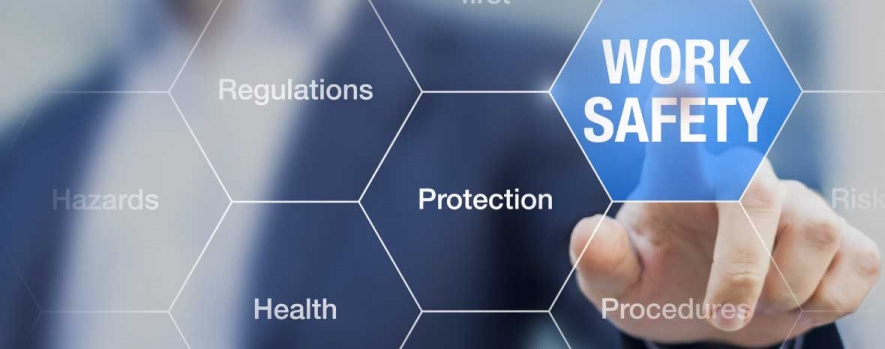
The importance of investigating a workplace injury, illness, or fatality cannot be understated. The long history of workers suffering debilitating conditions and loss of life has given rise to fully-funded government agencies being tasked with workplace safety.
And while agencies such as OSHA are tasked with safety oversight, investigating workplace incidents and taking corrective measures remains each individual company’s responsibility. While taking ownership is the first major step in creating a safe environment, these are critical investigative items necessary for maintaining the highest possible standards.
Recognize the Difference Between “Accident” and “Incident”
At first blush, the difference between using words such as “accident” and “incident” may seem pointless because many people consider them interchangeable. But the words leaders use in the workplace underscore the basic thinking and attitudes about policies, best practices, and safety.
One might consider spilling a coffee on your shirt or tripping because you forget to tie your shoelaces an accident. Those occurrences are worlds apart from a pallet falling off a forklift or a toxic chemical spill injuring a worker. Simply put, you wouldn’t task key stakeholders with investigating an “accidental” coffee stain on your shirt. You would bring significant resources to bear to investigate and update best practices in an effort to prevent repeat incidents such as broken bones or chemical burns.
When discussing issues that involve an workplace injury, illness, fatality, or even a near miss, it’s essential for supervisors to distinguish them as important safety events that can be corrected. That’s why defining the fundamental terminology around workplace safety matters.
Deploy Diverse Investigative Team
It has become almost standard practice for companies to task specific supervisors with looking into why incidents occur. However, it is gThe importance of investigating a workplace injury, illness, or fatality cannot be understated. A helpful guide to make sure your organization is fully prepared to avoid and investigate accidents.enerally in the organization’s best interest to include diverse perspectives.
While a supervisory team often provides keen insight into workplace incidents, they are inherently management representatives by nature. That may bring baggage to the table that includes minimizing company liability, among others. The benefit of bringing other stakeholders into the process is likely to deliver a more secure working environment. Machinery operators, labourers, and technical personnel also have a perspective on how company methods impact their daily safety. It’s not uncommon for a substantial gap to exist between a company’s safety policy, best practices standards, and their practical application in the workplace.
Sometimes it takes a harsh lesson for management and labor to effectively communicate and take corrective measures. Consider utilizing a worksite incident as an opportunity to hear multiple voices and do better going forward.
Preserve Incident Scene & Gather Pertinent Information
The investigative team’s first responsibility will be to secure the incident site and ensure it is safe. If possible, tape off the scene much like a police department might do to avoid further worker contact. This will also allow the incident team to photograph, videotape, and evaluate the space as it was at the time of the event. Consider these critical questions when compiling incident site data.
- What safety equipment or devices were being used when the incident occurred?
- What position were machinery or other safeguards in when the incident occurred?
- What was the condition of the space at the time?
- Did weather play a role?
- Was lighting or noise a factor?
- Were there blind spots or a lack of caution signs in place?
Beyond culling together a detailed record of the space, it’s also necessary to interview victims and others that played a role in the unfortunate incident. It may be in the investigative team’s best interest to have a questionnaire in place that asks salient questions in a non-confrontational fashion.
One of the long-standing impediments of workplace incident investigations is heightened emotions that lead to blame. If those involved believe the company is looking for a scapegoat, it may be challenging to conduct fact-finding effectively. That’s why level-headed questions and information gathering stands as a foundational element of improved workplace safety.
Conduct A Root Cause Analysis
Companies that fall under OSHA’s Process Safety Management or EPA’s Risk Management Program guidelines are tasked with completing an investigation into any workplace incidents that cause worker harm or may have resulted in the release of dangerous chemical agents. The underlying reasoning is that chemical spills and other workplace dangers could reoccur unless preventative measures are taken. The foundation of a proactive investigation is ascertaining the root cause of an incident.
The benefits of determining and analyzing the root cause of a toxic spill of another incident will ultimately reduce the possibility of future injury, sickness, or fatalities. So-called “near misses” can be particularly instructive because the at-risk individual can provide crucial information about how the circumstances evolved and how it could have been avoided. Companies often find that investing in workplace safety lowers the liability, improves productivity, and provides decision-makers peace of mind knowing they did their absolute best to keep valued employees out of harm’s way.
Conducting a root cause analysis is a vital and necessary process for improved workplace safety. In incidents involving hazardous spills, these are key questions an investigative team would be wise to get answered.
- How did the material spill?
- Did the spill occur as a result of workplace conditions?
- Did the hazardous material spill as a result of internal practices?
- Was the incident promptly reported?
- Were employees wearing personal protective clothing?
- Were appropriate cleanup procedures followed?
- Were the negatively impacted worker(s) wearing personal protective equipment?
To get to the hard facts about high-risk spills and other worksite incidents, OSHA publishes a fact sheet that includes a root cause analysis checklist. The federal agency suggests the investigative team utilizes a combination of the following tools to understand the underlying issues.
- Brainstorming
- Checklists
- Logic/Event Trees
- Timelines
- Sequence Diagrams
- Causal Factor Determination
At the end of your root cause investigation, the analysis should provide answers regarding the who, what, where, when, and how an incident happened.
Craft A Detailed Incident Report & Share the Findings
A successful workplace incident investigation would be rendered almost meaningless if it was not shared with change-makers and company personnel at large. This is a crucial point that decision-makers sometimes do not consider.
Having a detailed report in hand allows management to mandate change that improves workplace safety and appeases the insurance company. But the more employees who have access to the findings, the better individuals understand the reasoning behind modifications. This can be an absolute game-changer because many employees already believe they are working unnecessarily hard. Handing down more corporate directives only exacerbates that attitude. Transparency and inclusion show staff members that they are valued, respected, and provide clear reasoning why changes are needed.
Every organization’s best practices must include the use of personal protective clothing, defined safety policies, and procedures, as well as following through with forward-thinking incident investigations in the event of a catastrophe or near miss. Although the methods business leaders use to successfully operate an organization vary, safety is inherently a team effort.