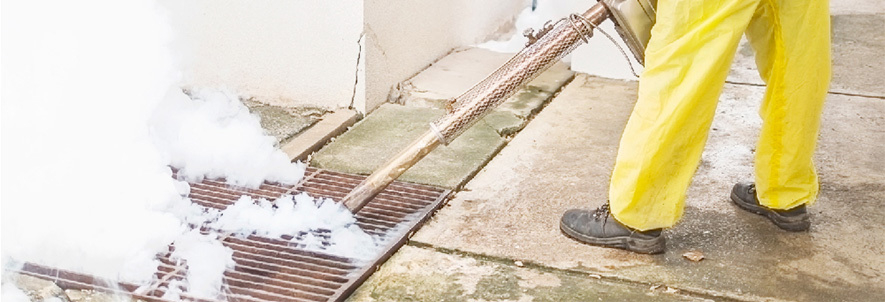
Best Practices for Vaporized Hydrogen Peroxide Sterilization
The use of vaporized hydrogen peroxide (VHP) as a workplace decontaminate has proven effective against health hazards that could compromise medical devices and food processing plants, among many others. The ability of vaporized hydrogen peroxide methods to eradicate bacteria, fungi, and some of the most lethal agents makes it an increasingly useful sterilization method.
However, the men and women who decontaminate enclosed spaces may be subjected to significant vaporized hydrogen peroxide hazards. It’s critical that employers follow stringent chemical usage guidelines, provide vaporized hydrogen peroxide safety equipment, and maintain a full inventory of disposable personal protective clothing.
What is Vaporized Hydrogen Peroxide?
Approved by the Environmental Protection Agency (EPA), vaporized hydrogen peroxide, also known as VHP or hydrogen peroxide fogging, is a sterilant that destroys microbial life forms such as bacteria, fungi, spores, and viruses. Using a low-temperature and deep vacuuming process, vaporized hydrogen peroxide decontamination is considered so powerful the EPA approved its use to eliminate anthrax in contaminated buildings. It has also been deployed to decontaminate spaces infected by avian influenza and Newcastle disease.
How is Vaporized Hydrogen Peroxide Generated?
Using a solution of hydrogen peroxide and water, generators convert the aqueous hydrogen peroxide into vapor. The vaporized hydrogen peroxide gas is then circulated at specific concentrations over items within an enclosed environment for a predetermined length of time. This is known as a sterilization cycle.
The mist typically kills bacteria and other contaminants within seconds. Once the cycle has been completed, the VHP is then vacuumed back through the generator. A catalytic converter breaks down the hazardous mist into water and oxygen at safe levels.
What Industries Use VHP?
Because VHP can be readily deployed in enclosed areas, it enjoys broad applications across numerous industries. The National Institute of Health indicates VHS has significant decontamination applications in dental and healthcare settings. Studies indicate it has proven effective in the elimination of Staphylococcus, Tuberculosis, SARS, the COVID-19 pandemic, and a wide range of other human health threats.
The portable nature of the VHP sterilization process makes it an effective tool to combat and contain outbreaks across industries and isolated contamination incidents. The medical and healthcare sectors commonly use it for the following.
- Medical Implants
- Electronic Devices
- Temperature Sensitive Products
- Pharmaceutical Packaging
- Medication Delivery Systems
- Cleaning N95 Respirators
Vaporized hydrogen peroxide has also gained traction in industries such as food processing. Its growing popularity is driven by tangible business advantages. However, VHP use poses a significant health risk if strict safety protocols are not followed.
Hydrogen Peroxide Sterilization Advantages and Disadvantages
Decision-makers are inclined to take advantage of the relatively low cost of using VHP compared to other sterilization processes. The technologies used are typically mobile and significantly reduce labor costs and manual cleaning.
Instead of hiring a cleaning crew to decontaminate surfaces manually, VHP is primarily a machine-driven process. Not only does it sidestep the cost of extensive manual spraying and wiping, but it has also proven more effective at deep cleaning, especially with sensitive devices. The vapor penetrates difficult-to-reach crevices to kill microorganisms that might otherwise remain.
Vaporized Hydrogen Peroxide Safety Risks
Although VHP has proven to effectively sterilize products and enclosed environments, it poses a health risk to the technicians who decontaminate spaces and returning workers. Concentrated exposure to hydrogen peroxide (H2O2) corrodes the skin, damages the eyes, and negatively impacts mucus membranes.
Those exposed to VHP often suffer conditions that include difficulty breathing, burning and watery eyes, irritated throats, skin conditions, and organ damage in some cases. Contact with even small concentrations causes discomfort and pain.
Due to the body’s ability to quickly break down hydrogen peroxide, workers are not considered at risk of conditions associated with long-term exposure, unlike asbestos or silica. But repeated exposure tends to have a cumulative effect on the body.
Ongoing exposure generally leads to respiratory tissue dysfunction and collapsed lungs in some cases. A single high-level exposure may result in lung damage even if the individual does not show signs within the initial 24 hours.
It’s important to also understand that workers returning to a sterilized space may be at risk of exposure. The generator used to vacuum up the solution may not necessarily retrieve all the hydrogen peroxide mist. Unless the space is adequately vented and a safe period of time passes, those entering the area risk exposure.
The substantial health threats to VHP technicians and returning workers are why organizations such as the Occupational Safety and Health Administration (OSHA), National Institute of Occupational Safety and Health (NIOSH), and American Conference of Governmental Industrial Hygienists (ACGIH) have developed rigorous workplace standards to manage vaporized hydrogen peroxide hazards.
Best Practices for VHP Usage: Hydrogen Peroxide Fogging Safety
Technicians conducting decontamination using vaporized hydrogen peroxide work at a critical disadvantage. The solution is odorless, colorless, and cannot be detected unless workers are provided with gas monitors.
The same holds true for returning workers who might otherwise assume the confined area is free of harmful chemicals. The ACGIH, OSHA, and NIOSH all agree upon the average daily occupational exposure limit of 1 ppm. Concentrations above 75 ppm are considered immediately dangerous to life and health.
That’s why employers are tasked with providing technicians with detectors and personal protective equipment during the sterilization process. These sensitive gas monitoring devices should also be deployed in areas at the conclusion of the decontamination. An alarm typically alerts workers of existing vapors and protocol dictates putting on respirators and taking steps to ventilate the space. Permanent detectors are prudent in areas that routinely undergo chemical sterilizations.
Workplaces prone to aerosolized hydrogen peroxide hazards require adequate ventilation systems, windows that allow fresh air into the area, and HVAC systems with filters. Promptly cleansing breathable air reduces the potentially harmful effects of VHP on the eyes, skin, and lungs. Perhaps most importantly, vaporized hydrogen peroxide safety calls for employers to maintain a full inventory of the following personal protective equipment and disposable clothing.
- Full-Cover Protective Suits: VHP workers need lightweight coveralls that provide protection from the top of the head to the ankles. Disposable coveralls must meet OSHA standards in terms of chemical splash resistance. These personal protective clothing items must be worn before handling chemical compounds or entering a biohazardous space.
- Shoe Coverings: Because the mist settles on shoes and flooring, vaporized hydrogen peroxide hazards must be addressed at every level. The best coveralls can be accessorized with shoe/boot coverings that seamlessly cover the ankles and feet. This practice prevents workers from coming into passive contact with hydrogen peroxide after sterilization has been completed. For coveralls without attached booties, consider splash-proof shoe covers.
- Protective Gloves: Any skin contact results in chemical burns and vaporized hydrogen peroxide potentially entering the bloodstream. Coveralls with taut elastics at the wrist can overlap disposable protective handwear.
- Face & Eye Protection: It’s essential for technicians to wear commercial-grade eyewear when deploying vaporized hydrogen peroxide. A full-face shield is also important to prevent mist from accumulating on the breathable mask and face.
Vaporized hydrogen peroxide safety also calls for technicians to wear fit-tested respirators when dispensing the mist. Respirators should remain in place throughout the vacuuming process as well. Employees entering decontaminated areas would be well-served to exercise caution and use disposable masks to ensure safety.
Workers require a complete inventory of personal protective equipment and disposable clothing options to protect against vaporized hydrogen peroxide hazards. But the benefits of effectively eliminating many of the most dangerous human health dangers make VHP an essential method to prevent tainted medical equipment and food contamination.