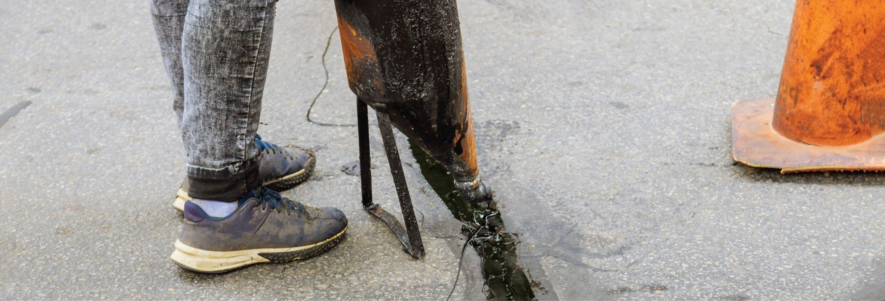
Asphalt is one of the most widespread materials used in modern construction. Everything from driveways to parking lots to roads uses asphalt, illustrating how integral it is to society.
But why does asphalt work so well? Well, part of the reason is sealcoating. This material helps protect the surface from various elements such as weather and wear and tear. This article will dive into the world of sealcoating, including how it works, why it's used, and its potential health and safety implications.
What is Sealcoating?
Asphalt is made by mixing rocks, stones, or gravel with a binding agent. This agent is often petroleum-based, and it's called asphalt cement. Sealcoating refers to the process of adding a thin liquid layer of protection to the asphalt cement. There are multiple types of seal coats, which we'll discuss later. Sealcoating is designed to prevent asphalt degradation by various elements, such as rain, water, UV rays, oil, and gasoline.
The seal coat itself is made of an emulsion of water, silica sand, polymer additives, and other fillers and solids. Workers spread the emulsion over the asphalt surface with a spray, brush, or squeegee so that it can fill in the various cracks and seal them.
Without regular maintenance and seal coating, asphalt can become brittle and break down. The material can also get stained easily by other petroleum products like gasoline or motor oil. Over time, the surface will wear down and erode, creating potholes.
On average, companies should seal coat their asphalt surfaces every two or three years to keep them in excellent condition.
Benefits and Limitations of Sealcoating
While sealcoating is highly beneficial, it's not magic. Here are some pros and cons of using sealcoating on asphalt.
Pro: Sealcoating Extends the Life of Asphalt
On average, asphalt can last between 10 and 35 years, depending on its usage. For example, an asphalt road will wear down much faster than a driveway with minimal traffic. With regular sealcoating, these surfaces can last well over 30 years with minimal repair and maintenance needed.
Con: Sealcoating Can't Repair Existing Damage
If the asphalt already has cracks and holes, no amount of sealcoating can fix it. This material is designed to prevent damage, not repair existing problems.
Pro: Sealcoating Helps Save Money
Overall, it's much more expensive to fill in a pothole than it is to spray and apply sealcoating. Regular application every two to three years can help limit the number of patches and fixes necessary for asphalt roads and surfaces.
Con: Sealcoating Takes Time to Cure
Sealcoating requires at least 24 hours to dry. Also, in areas where rain is common, workers have to wait for a dry spell before applying a new seal coat. Cars also can't be on freshly coated pavement for 24 hours after applying.
Pro: Sealcoating Helps Melt Snow and Ice
In winter conditions, frozen roadways can be a considerable hazard for drivers and pedestrians alike. Sealcoating helps prevent freezing by repelling water. So, it takes much longer for roads to get icy, making driving conditions safer.
Types of Seal Coats
There are a few different methods used for sealcoating. Here's a breakdown of each one.
Coal Tar Emulsion
This option is the most common because it's durable and lasts for up to five years. It's naturally resistant to UV light and water, and it binds to asphalt quickly and reliably.
That said, because this emulsion uses coal tar, it does have adverse environmental and health effects. As a result, some areas have banned its use, forcing companies to switch to more eco-friendly solutions. Coal tar is also naturally gray, so it can make asphalt look more faded.
Asphalt Emulsion
In this case, the seal coat is made from asphalt and water. The main advantage is that it can help make the surface look brand-new, and it helps fill in cracks and small holes. Basically, workers are spreading a new, thin layer of asphalt over the old one.
However, since the new surface is the same as the old, it's still susceptible to the elements and can wear down relatively quickly. Also, adding more and more layers doesn't work well in the long run, as roads can get bumpy and uneven over time.
Acrylic Seal Coat
While asphalt and coal tar are relatively affordable, acrylic seal coats are the most expensive. This option offers high-quality protection like coal tar and without the environmental dangers. However, due to its high cost, acrylic seal coats are primarily used for small parking lots or sports courts. The price tag is too steep for large-scale projects like roadways.
Oil-Based
Although oil-based seal coats are not advantageous, some people still use them. These coats take the longest to dry and cure, sometimes taking up to seven days. They also produce off-putting smells, and they don't protect well against UV rays. However, oil is naturally water-repellant, which is the main benefit.
An Overview of the Sealcoating Process
Whether it's a road, parking lot, or driveway, the sealcoating process is pretty much the same across the board. Here's how it works.
Step One: Pay Attention to the Weather
One issue with sealcoating is that the climate conditions have to be just right. It can't be too hot or too cold, and the humidity level has to be relatively low. Also, if rain is in the forecast within 24 hours, workers should postpone the project until it is drier.
Step Two: Prep the Surface
For the sealcoating to bond effectively, there can't be any dirt or debris on the surface. So workers will need to sweep and clear any noticeable materials before sealing.
Step Three: Remove Petroleum Stains
As we mentioned, petroleum products can bond to each other easily. So, asphalt can get stained by gas and motor oil. Unfortunately, these stains can prevent a secure bond with the new coat. So, workers will flash heat these stains to burn off the petroleum, creating a smoother, purer surface.
Step Four: Fill Any Large Cracks
Since sealcoating doesn't fix cracks and holes, workers must fill these gaps manually before starting. The best option is to use hot tar sealant or something similar that will last a long time.
Step Five: Spray the Sealcoating
Spray hoses are the fastest and most economical option, but they can also be messy. We'll discuss the best sealcoating clothing for workers to prevent exposure to harmful elements. Workers should spray a thick, even layer of seal coat across the entire surface, including the edges.
Step Six: Smooth Out Any Imperfections
After spraying, workers can spread the seal coat around with brushes and squeegees. Doing this ensures that the material fills in all cracks and gaps within the asphalt. This step also ensures that there are no bumps or other imperfections in the finished product.
Step Seven: Let Dry
Depending on the type of seal coat used, workers should let it dry for between 24 and 48 hours. This step is crucial as it allows the coating to cure and bond with the asphalt. Otherwise, the layer can get removed, undermining the whole process.
Health and Safety Issues With Sealcoating
The main health-related danger of working with sealcoating is that the materials are often carcinogenic. So, if workers get exposed to them through skin or lung contact, they can develop cancer and other illnesses. One instance probably won't do anything, but repeated contact with these toxins can lead to long-term damage.
Coal tar emulsions are the leading contributor to cancer and other health problems, but other materials have toxic chemicals as well, making them hazardous to workers and the environment.
Safety Practices for Working with Sealcoating
Since seal coats are toxic, it's crucial to follow standard health and safety guidelines. Here are some best practices for sealcoating:
- Train Staff and Supervisors- All workers and managers should be aware of the potential dangers before starting a project. Everyone must be trained on how to use sealcoating equipment, including sprayers, brushes, and mixers.
- Offer Sufficient PPE- Workers should be covered from head to toe while on the job. Standard sealcoating PPE should include boots, coveralls, gloves, safety glasses, and a helmet. While spraying, employees should wear face masks and shields to prevent breathing in harmful fumes or particles. While the coat is fresh, workers should still wear face masks since the material can still release fumes for several hours.
- Follow Manufacturer Guidelines- Spray machines can get clogged or stop working suddenly. Workers should know how to fix these issues without putting themselves or others in danger.
Get Your PPE From International Enviroguard
Protect your workers from on-the-job hazards with the best personal protective equipment available. International Enviroguard has a vast selection of disposable coveralls to keep everyone safe and comfortable.