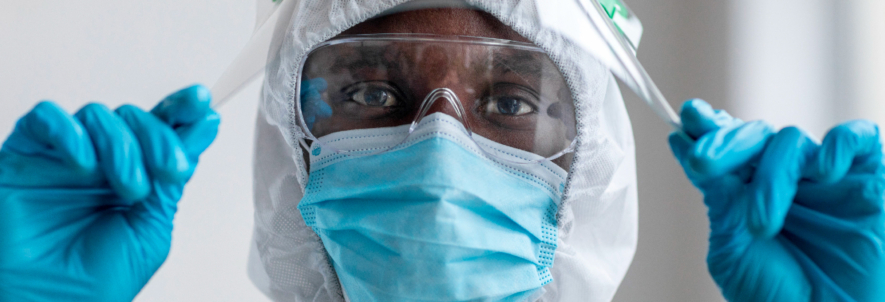
The workplace safety agency tasks companies with following strict PPE safety and compliance guidelines to ensure men and women finish their shifts without incident. A National Institute of Health study indicates that more than 40 percent of workers did not wear PPE, and these are stigmas associated with such products.
- Discomfort: Approximately 78 percent said PPE was too uncomfortable.
- Information: About 72 percent said they didn’t know how to use PPE.
- Wrong Sizes: Nearly 70 percent said the protective clothing did not fit correctly.
- Overheating:Nearly 70 percent said it made their body excessively hot.
Other startling statistics show that two-thirds of employees indicated that PPE and disposable clothing products were simply not made available to them. Of the companies that maintained a mandatory inventory, more than half of staff members took the items off while on the job. The trend of non-compliance is unsustainable for employers and employees alike.
Employers Face PPE Safety and Compliance Headwinds
It’s safe to say that the majority of contractors, manufacturers, and other industries that include workplace hazards do their best to provide PPE and disposable clothing for their crews. But pandemic-driven shortages and ongoing supply chain disruptions have made stockpiling protective gear an uphill battle. In fact, 71 percent of industry leaders said they experienced order fulfillment delays.
Coupled with frustrating back orders, inflation hasn’t just spiked the cost of groceries and housing. Safety managers and CFOs are stunned by the unreasonably high price of PPE some companies are charging.
As organizations search for domestically made protective clothing and equipment suppliers to overcome dwindling supplies, they face another problem — regulatory fines. In January, OSHA ratcheted up the fines for PPE violations to $460 for a non-serious first offense and $1,152 the second time.
For serious violations, employers face $16,131 per violation, and repeat violators could get hit with a $161,323 OSHA penalty. Along with potentially debilitating fines, not having the right PPE increases the risk of injury, and that brings hefty medical bills, worker’s compensation premiums to shoot up, business liability insurance to rise, and a steady stream of lawsuits will inevitably follow.
These issues are likely to push companies to overpay, in some cases, to ensure they have safety clothing and equipment on-site. Without the right PPE and disposable clothing supplier, the cost of doing business cuts into profit margins.
How to Overcome PPE Noncompliance
The responsibility for regulatory compliance falls squarely on an employer’s shoulders, regardless of whether PPE is available or why workers fail to use products correctly. Companies need to go the extra mile to ensure an appropriate inventory of protective clothing and equipment is available and find ways to encourage consistent usage. These are steps on how to overcome PPE noncompliance.
Conduct Hazard Assessments
Based on OSHA 1910.132(d), every employer must conduct a work environment hazard assessment to determine what hazards are present and the level of risk workers face, if any. Should the landscape, equipment used, or other conditions call for PPE, the employer must choose an effective product to protect workers’ health and safety.
What’s interesting about the OSHA mandate is that it directly addresses one of the key reasons why crew members do not wear PPE — discomfort. The regulation expressly states PPE “properly fits each affected employee.”
Hazard assessments involve wide-reaching factors that include temperature, airborne threats, chemical agents, and others. Your industry or business may be required to produce a written hazard assessment. However, even if it is not mandated, having a clear, concise articulation of the potential hazards and why you selected specific PPE can prove useful if OSHA conducts a walk-through.
Address Appropriate Fitting Protective Clothing
It’s important to keep in mind that specifically fitting disposable personal protective clothing does not come as a one-size-fits-all. Employers also need to account for the fundamental differences between men’s and women’s clothing contours.
In 2023, the number of women working in construction hovered around 11 percent, the highest in decades. The percentage of female commercial truck drivers exceeds 12 percent, and more women are taking positions in manufacturing.
These once-male-dominated sectors are experiencing gender diversity that impacts the culture and PPE selections. Not only do personal safety clothing inventories need to address the differences between women and men, but they must also adhere to the following.
- Avoid gaps in protection coverage that could invite exposure.
- Provide relatively unrestricted movement whenever possible.
- Conform to the individual’s body type to ensure comfort while performing duties.
- Avoid loose sleeves, pant legs, and other areas that could get caught in machinery.
- Eye protection cannot obstruct views or fog up.
- Ear protection must reduce anticipated decibels without harming the auditory canal.
Addressing form-fitting PPE starts with choosing a clothing line that offers men’s and women’s options and a variety of industry-suitable products. The next-gen technologies and advanced materials being used in top-tier disposable clothing lines provide breathability without sacrificing worker protection.
Decision-makers would also be well served to consider whether the manufacturer offers accessories that can be seamlessly integrated into a base item, such as a chemical splash suit or coveralls.
Offer PPE Safety and Compliance Training Programs
Overcoming PPE noncompliance starts with connecting the dots between workplace hazards and the safety clothing and equipment provides. For instance, highlight the difference between coming into contact with an industrial acid wearing a long-sleeve street shirt versus chemical splash-resistant coveralls.
The former provides less than zero protection because the toxic agent will soak into the fabric, unnecessarily adding injuries. The correct PPE, by contrast, prevents skin contact, avoiding a painful trip to the emergency room.
Although such examples may seem like common sense, not everyone makes a clear connection between Point A and Point B. This type of safety awareness training may seem remedial, but it hits home. When people make strong mental connections, they are more likely to wear PPE throughout their shift.
A significant portion of any PPE safety and compliance program should be delegated to properly fitting products. Emphasize the company orders a variety of sizes for women, men, and different body types. Ask team members to try on a few sizes and accessories to determine which fits best. Highlight the need for mobility and snug comfort that is not overly tight. You may want to integrate a movement test, such as being able to easily bend over, lift a box, and set it on a shelf.
Heat exhaustion also represents a clear and present danger for people who work near furnaces and outdoors during the summer months, among others. Consider having crew members don protective clothing and accessories in an environment that simulates standard workplace conditions. It’s better to make adjustments and know the best option, before trial-and-error places someone in harm’s way.
A robust PPE safety and compliance program typically presents hard data to underscore the pragmatic approach to encouraging usage. According to OSHA, a successful PPE program reduces the number of injuries and work-related illnesses by 37.6 percent. Upwards of 14 percent of on-the-job injuries leave hard-working community members totally disabled, largely due to not wearing PPE.
When developing a risk assessment and selecting protective clothing, it’s essential to connect with an organization that can supply gender and size-appropriate products on time and at a reasonable cost.