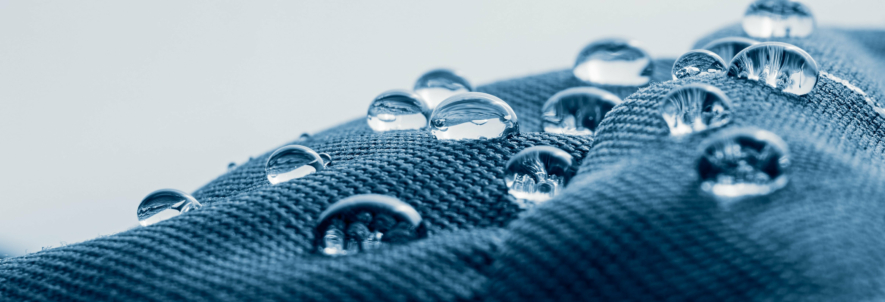
Safety managers tasked with building an inventory of disposable personal protective clothing may not necessarily be selecting the best product for their valued employees. That’s largely because the testing standards used to determine critical safety are often confusing.
Understanding how to calculate safe- wear times for chemical resistant clothing is not always what it seems. For example, what is the difference between permeation and penetration? And does your organization provide protective wear that truly insulates workers from hazardous chemicals?
What Does Chemical Suit “Permeation” Really Mean?
When personal protective clothing products are tested, permeation metrics involve the rate at which these harmful agents end up on the human side of the barrier. Companies typically do not consider rips, tears, or design faults when determining the rate of permeation. Rather, it’s a natural progression of cells interacting with others as they migrate through the outer layer of a chemical suit.
In this regard, permeation moves through what appears to be a solid barrier that may deceivingly lead quality control leaders and safety managers to believe they have the best possible protective wear. The fact remains that permeation rates are critical indicators of actual protection from dangerous substances.
Although permeation at a micro level cannot be prevented, testing results can help guide disposable protective clothing selections. These are factors that go into standard permeation metrics.
- Rate of seepage through the chemical-resistant fabric.
- How long the fabric comes in contact with a chemical agent.
By multiplying these two factors, you arrive at what is known as the “Cumulative Volume.” For example, a rate of permeation of 10 micrograms per minute multiplied by 120 minutes equals a Cumulative Volume measurement of 1,200 micrograms. That also means that after two hours, the suit wearer experiences 1,200 micrograms of a contaminant. Environmental conditions such as temperature and humidity may also exacerbate the rate of permeation.
How Does Chemical Suit “Penetration” Work?
Knowing a chemical suit’s penetration rates is a straightforward way of understanding its safety value. Penetration is determined at the macro level as chemical agents pass through a suit’s protective barrier. Rather than reflect cellular-level migration, penetration looks at quality issues such as gaps, holes, and the structural integrity of disposable personal protective clothing.
Penetration rates effectively deal with the quantities of chemicals that infiltrate what is supposed to be a secure barrier. Considered a product defect, manufacturers have an opportunity and responsibility to fix and address these hazards. Although protective clothing designers and manufacturers routinely use visual inspections, the International Organization for Standardization (ISO) establishes the penetration guidelines. A penetration test typically involves the following.
- Place the protective fabric at a 45-degree angle in a gutter lined with an absorbent material.
- Pour 10 ml of the test liquid every 10 seconds on the fabric.
- Liquid that penetrates within 1 minute is noted by penetration percentage.
- Liquid that fails to penetrate the material is noted as a percentage of repellency.
This assessment provides a balance of two metrics — repellency and penetration — and is placed in three performance classes. Class 3 materials enjoy a repellency rate of 95 percent against 1 percent penetration and 4 percent unaccounted for testing loss.
Why Does this Difference Matter in Relation to Chemical Resistant Clothing?
Disposable personal protective clothing products with evident penetration are unsuitable for hazardous chemical environments. The fact that a single spill, splatter, or incident can result in skin contact renders the chem suit unsafe. When processing information to arrive at the best possible protective clothing options, it’s critical to place permeation under a microscope.
One of the main ways for safety managers and product buyers to understand worker protection is through an industry term called “Breakthrough.” Also known as “Breakthrough Normalization,” this speaks to the product’s class. It indicates how long it takes for chemicals and hazardous liquids to pass through the safety suit and negatively impact its wearer.
How to calculate safe- wear times for chemical resistant clothing is based on Normalized Breakthrough rates under the EN 14325 standard. It’s the time taken until 1.0 microgram per centimeter squared permeates the material per minute. These are Normalized Breakthrough classifications for protective clothing.
- Class 1: 10 minutes.
- Class 2: 30 minutes
- Class 3: 60 minutes
- Class 4: 120 minutes
- Class 5: 240 minutes
- Class 6: 480 minutes.
Based on this assessment, companies that require employees to perform tasks in environments with chemical agents would be wise to choose disposable protective clothing that lasts for an entire shift or for the full duration of a task-based application. Task-based applications typically do not require an entire shift to complete; they are usually a specific, short-term task that requires bodily protection. Examples include tasks such as mixing or preparing chemicals or cleaning a chemical spray tank.
Part-time workers could, conceivably, adorn Class 5 chem suits that provide protection for up to 4 hours. Full-time employees would logically need disposable clothing with safe-wear times of 480 minutes, the equivalent of 8 hours. It’s also important to keep in mind that top-tier safety suits may be rated as Class 6 even though no breakthrough occurs within an 8-hour time frame.
How To Determine the Toxicity Limit of Workplace Chemicals
The impact of permeation and penetration does not happen in a vacuum. These metrics relate to real contact and not every chemical has the same short- or long-term effect on employee health and well-being. Decision-makers would be well served to review chemical agents that are in use and evaluate their “Toxicity Limit.”
The Toxicity Limit technical term refers to the amount of contact with a specific chemical it takes to cause bodily harm. Toxicity Limits are usually estimated at one square centimeter of surface area. Of course, chemicals possess vastly different toxicity levels and small amounts of the most poisonous agents can cause debilitating health conditions. That’s why permeation rates must be coupled with industry standard toxicity limit designations, such as the following.
- Highly Toxic: The toxicity limit for highly dangerous chemicals is set at 20 micrograms per square centimeter.
- Toxic: This designation equals 75 micrograms per square centimeter.
- Other Chemicals: A wide range of chemicals that require chemical suit protections involve toxicity limits of 150 micrograms per square centimeter.
Chemical manufacturers and product users generally label vats and containers accordingly to alert workers of their danger. Whenever toxic agents are present or create a risk, appropriate disposable protective clothing is mandated by the Occupational Safety and Health Administration (OSHA) and other agencies for worker safety.
What are the Benefits of Considering Safe-Wear Times?
The importance of taking safe-wear times into account when choosing leading chemical suits cannot be understated, even though these rates deal with seemingly minute amounts of toxins. But people who work in chemical plants and other environments experience a cumulative effect.
Over time, minuscule amounts of a cancer-causing agent build up in workers. Trace amounts of such agents may also find their way into the homes of working families, harming small children who may be at increased risk. Below are other benefits for safety managers, human resources professionals, and product buyers to consider.
- Meet OSHA and other health and safety compliance regulations.
- Maintain the health and safety of employees and their families.
- Minimize insurance premiums and potential civil lawsuits.
- Reduce the number of sick days or call-outs due to exposure.
Companies have an ethical obligation to workers and their families to provide a complete inventory of secure chemical suits and accessories with the highest ratings. When safety managers and product buyers know they have built a comprehensive inventory of disposable personal protective clothing, everyone feels better about meeting their responsibilities. International Enviroguard manufactures and distributes a complete line of disposable protective clothing and accessories that exceed industry standards.