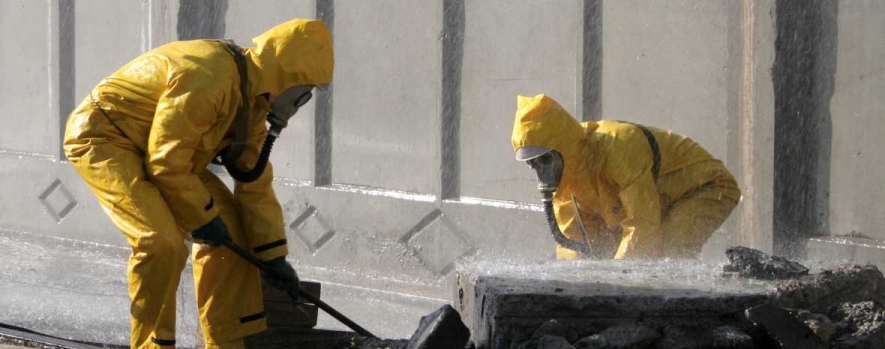
Workplace and environmental contamination present a very real danger. But the risk is often far more wide-reaching than many people think. That’s largely because we have become accustomed to media coverage of these critical events that are tied to those immediately exposed.
Unless the crisis has global significance such as the Fukushima nuclear plant disaster in Japan, rarely are peripheral exposures identified. But those who work in potentially hostile environments know that first responders, Hazmat crews, and others tasked with clean up and contamination control are not just in harm’s way, they work in imminent danger.
That’s why personal protective equipment (PPE), including personal protective clothing (PPC), has been mandated by agencies such as the Occupational Safety and Health Administration (OSHA), among others. To better understand the necessity of PPE, consider the on-site decontamination methods required to eliminate the health and safety risks associated with contamination events.
Standard Decontamination Methods
It’s important to keep in mind that the process of decontamination is not an abstract concept. It is performed by men and women who make an informed decision to put themselves at risk for the safety of their valued community members. Although many go unheralded for their determined bravery, it’s essential they are provided with the highest quality PPC while eliminating contamination threats. These are routine decontamination methods employed to restore environmental safety.
- Physical Cleansing: This initial step requires contamination responders to remove liquid and solid materials from the ground, floor, workplace equipment, and other items in the physical environment. Safety specialists often come into direct contact with hazardous materials during this process.
- Ultrasonication: This process utilizes high-frequency sound waves to create and capture liquid bubbles. It is a common decontamination method employed in health and beauty sector laboratories. Although considered effective in those and other industries, splashing liquid and airborne contaminants are prevalent. Only certified facemasks and breathing equipment can deliver lung protection.
- Microorganism Disinfection: This decontamination step targets pathogens not seen by the naked eye. The goal is to reduce these hazardous organisms to a low enough level that they no longer pose a health and safety risk. The unseen nature and potential to throw off spores make this decontamination process inherently dangerous. Total PPC coverage is necessary to avoid skin, open wound, or breathing contact.
- Antisepsis: This process generally refers to removing infectious elements by using powerful chemicals. Decontamination workers face a dual-threat risk of exposure to the pathogen and coming into contact with the dangerous chemicals. PPC items such as gloves and body coverage to avoid contact with splashes remains a safety necessity.
- Wet Heat Sterilization: Sterilizing and disinfecting workplace and environmental contamination by targeting intensely heated liquids remains an effective method for eradicating dangerous microorganisms. While the contamination control process often involves steam and brings about effective sterilization, decontamination workers may be exposed to high-temperature materials. Autoclaving is a commonly employed heat sterilization method that delivers moist, hot steam, followed by vacuuming. Bodily contact is often unavoidable.
- Dry Heat Sterilization: Delivering intense heat has proven effective in reducing and eliminating microorganism dangers. Cleanup crews generally employ a temperature-time process that ranges from 330-375 degrees Fahrenheit for 30-120 minutes. Personal protective equipment must be appropriately rated to minimize the risk of skin and facial burns.
Cleanup crews and decontamination specialists make strategic decisions about which method is required to bring about an effective result. But with each decision to render a workspace or open-air hazard harmless, contamination responders must have the best possible PPE. In each case, the only thing standing between the danger and the frontline specialist is the protective gear that covers their face, torso, and extremities. While all of the methods used to secure workplace and community safety come with a risk, perhaps none is more dangerous than chemical disinfection.
Chemical Disinfection Presents Risks for Decontamination Specialists
Chemical-based disinfection methods rank among the most prevalent in manufacturing, agricultural, and other sectors. The machinery used often attracts dust, grime, and byproducts of the primary materials. For instance, a meat processing plant must undertake the highest decontamination protocols of equipment on a regular basis to ensure food safety.
Government oversight remains quite stringent in this and other industries. Companies are well aware that a failed inspection can shut down an operation and cause substantial revenue losses. Those are among the reasons why powerful chemicals are used to eliminate even the most remote possibility of contamination. But at the same time, these potent commercial products create an imminent health and safety danger to the workers tasked with routine cleanup. Consider these harsh chemicals commonly used to decontaminate commercial machinery and workspaces.
- Bleach: This prevalent decontaminant product can burn skin and damage the human eye.
- 80-Percent Alcohol: Often used to remove soil from equipment, its rapid evaporation makes it one of the less risky products used in commercial settings. However, it can be highly flammable at this strength.
- Chlorine: This commonly used chemical in swimming pools can be increasingly dangerous to inhale when used in concentrated decontamination efforts.
- Formaldehyde: This product is used as an effective disinfectant in both a liquid and gas form. It poses long-term cancer and asthma risks when inhaled and has been linked with severe skin disorders.
- Hydrogen Peroxide: Considered widely effective against invasive bacteria, fungi, viruses, and spores, it can prove fatal if ingested and may slow down the body’s ability to heal if users come in contact with it.
There are numerous harsh chemicals used in industries to maintain cleanliness and eliminate potential contamination. Agencies such as OSHA publish strict guidelines that state PPEs and PPCs are required when tasking responders or industry personnel with decontamination efforts. It’s imperative that decision-makers and frontline decontamination workers alike are fully outfitted with crucial safety gear and clothing at all times.
Necessary Personal Protective Clothing During Decontamination Efforts
It’s critical that decontamination specialists and cleanup crews are fully outfitted with industry-appropriate PPC. There are no legitimate half-measures or minimizing the necessity of complete protection. When tasked with decontamination, frontline workers must have the following certified safety gear.
- Chemical Resistant Boots
- Protective Gloves
- Respirators
- Safety Glasses
- Hard Hats
- Shoe Covers
- Disposable Knee Pads
- Chemical Coveralls
- Totally Encapsulating Suits
Although the commonly held perception about cleanup efforts tends to run one way, the dangers contamination responders and routine cleanup workers face remain multifaceted. Not only do the people who maintain health and safety for our communities risk harm from pathogens, they also must be adorned with personal protective gear to insulate them from the agents used to eliminate dangers.