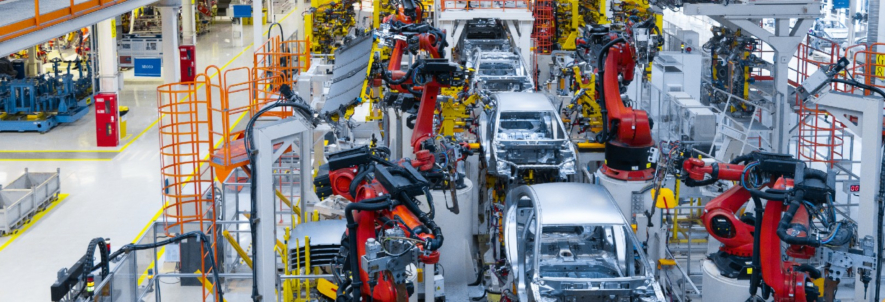
Since the U.S. and other countries came to a near economic standstill during the pandemic, growth has been relatively steady, and manufacturing trends show there is plenty of room for human beings alongside AI and automation. After dipping to $5.7 trillion in 2020, future trends in manufacturing industry growth indicate the U.S. will surpass the 2023 high-water mark of $6.42 trillion and increase to $6.74 trillion by 2028.
Automotive parts, consumer goods, and materials manufacturing industry trends all show upward mobility from the 2023 output. The number of year-of-year jobs in occupations involving production is also projected to hover around 933,000 through 2028 and beyond, according to the Bureau of Labor Statistics.
Driven by supply and demand, as well as government incentives, some sectors will rise while others decline in the coming years. Regardless of which way they are trending, the need for effective personal protective equipment and disposable clothing remains constant.
Government Spending Influences Manufacturing Industry Trends
Although disagreement persists regarding the wisdom of tax-and-spend policies, recent federal laws are expected to encourage significant growth in specific sectors. More frontline workers will be needed to fill growing industries that produce select products. Additional construction materials, tools, and personal protective equipment will also be required.
Infrastructure Investment and Jobs Act
The $1.2 trillion Infrastructure Investment and Jobs Act throws tremendous incentives behind sustainable energy projects and certain types of manufacturing. The law authorizes an additional $550 billion in annual government spending above the thresholds that existed when it passed. These are industries that are expected to spur job creation and augment manufacturing industry trends.
- Road Construction and Materials Production
- Battery Electric Car Manufacturing
- Solar Energy Product Manufacturing and Installation
- Electrical Power Production
- Transitioning Public Transportation to Zero-Emissions Vehicles
- Seaport Expansion and Waterway Dredging
The Infrastructure spending package also invests money in cleaning up Superfund sites and brownfields. Upwards of $21 billion was allotted to support remediation and cleanup efforts that will require training workers about hazardous materials, best practices, and outfitting workers with disposable personal protective clothing and equipment.
Creating Helpful Incentives to Produce Semiconductors (CHIPS) and Science Act
Manufacturing plants discovered they were overly reliant on Asian-made semiconductors during the pandemic. When major chip-makers shuttered, the supply chains quickly dried up.
In an effort to onshore the manufacturing of these tiny electronic components needed to complete automobiles and most electronic devices, the federal government passed the CHIPS and Science Act, which provides tax incentives and makes money available for companies to build or expand semiconductor manufacturing facilities. This is how the money is reportedly being allotted.
- Offers $52.7 billion for semiconductor research, development, and workforce training.
- Includes $39 billion in semiconductor manufacturing incentives.
The federal spending and incentives policy is expected to help increase manufacturing jobs. According to the White House, onboarding policies have helped produce 642,000 manufacturing jobs from 2021 to 2022. Semiconductor manufacturing in the U.S. is expected to be an up-and-coming growth industry.
U.S. Manufacturing Industry Metrics
While government incentives and tax-revenue incentives are helping to increase policy-driven manufacturing, the private sector is largely indebted to the law of supply and demand. With the exception of the sluggishness experienced during the health emergency, the construction sector has shown persistent resiliency.
Driven by a national housing shortage, investment in residential builds soared from $247 billion in 2012 to a record $939 billion in 2023. Commercial builds have steadily risen from $284 billion in 2012 to $499 billion in 2022. A consistent growth industry, the manufacturing of lumber, tools, and materials such as metal roofing shows little signs of waning.
These industries are also expected to experience significant revenue growth in the U.S. through 2025.
- Solar Power is expected to grow by 26.4 percent.
- Hybrid and Electric Car Manufacturing is expected to increase by 22.4 percent.
- 3D Printer Manufacturing is anticipated to grow by 19.8 percent.
- Ship Building to rise by 15.6 percent.
- Wind Power to increase by 12 percent.
Ranked among the fastest-growing sectors in terms of revenue, the solar power industry is expected to produce nearly 7,000 new jobs and more than 500 businesses over the next five years. Not surprisingly, industries that are already experiencing a decline in demand are expected to slow even further.
Big Tobacco, once a prominent agricultural and product-making niche, has lost its appeal. Its workforce is expected to be cut in half in the coming years. According to the U.S. Career Institute, manufacturers of magnetic optical equipment and clothes-makers are also likely to drop in the U.S. by 50.4 percent and 35.7 percent by 2031, respectively.
Changing Manufacturing Driving Shift in Worker Skills
According to the National Association of Manufacturers, upwards of 13 million people work in approximately 240,000 manufacturing operations in the U.S. These companies will reportedly need more than 4 million skilled and unskilled workers by the end of the decade. Complicating new hires is the fact that advancements are tasking employees with learning new skills to co-exist with emerging technologies.
Perhaps no industry articulates this new normal better than the truck transportation sector. Self-driving semi-trucks currently require a human CDL holder to sit in the cab while AI software negotiates interstates and highways. Most industries are unlikely to have a real person to simply supervise AI, but employees will have to coexist with machines.
Manufacturing businesses are taking proactive measures to up-skill current staff members and offer training programs to onboard new hires. The National Association of Manufacturers indicates that 60 percent of manufacturing organizations are augmenting existing training programs or creating new ones to close the growing skills gap.
The automotive industry, for example, has emerged as a leader in integrating robotics that requires technicians to make adjustments and reset software programs. While the influx of technology and other manufacturing industry trends may not necessarily appear to change the way safety is addressed, companies will also be charged with meeting changing regulations.
Future Trends in Manufacturing Industry Impact Worker Safety
Companies that engineer and manufacture personal protective equipment and clothing have also been quick to leverage technology to improve products.
For instance, the high-efficiency particulate arrestance (HEPA) filter was initially created to protect soldiers during World War II. Today, it serves the health and well-being of workers in hazardous material remediation and other environments. That being said, these are ways workplace safety adjustments continue to evolve as manufacturers adopt new technologies, devices, and increase their workforce.
- Noise Protection: The increased use of robotics in automotive plants and other environments tends to raise decibel levels. Automation in welding, forging, assembly, and palletizing creates significant noise that can negatively affect human ears. More than a quarter of factory workers are reportedly exposed to noise levels that require sound-dampening protective equipment.
- Eye Protection: The need for clear protective eyewear cannot be understated. The machines companies rely on to improve efficiency and productivity pose a danger to workers. Not only do employees need to wear protective eyewear to prevent injury from flying particles or infection from dust, but they also need to see the field in front of them at all times. Moving machine parts puts people in harm’s way, which is why anti-fog goggles are essential.
- Hand Protections: The transition from manual labor to electrified robotics increases the amount of power in the workplace. One prime example is the manufacturing of battery-electric vehicles. Reliance on lithium-ion batteries, in conjunction with machine automation, means the manufacturing plant has charged materials at multiple levels. Protective rubber gloves are now critical throughout the environment to avoid electric shocks and severe burns. Given this and other manufacturing trends, personal protective glove sales are on track to surge by 11 percent by year’s end.
Workers who are likely to benefit from demand, as well as government incentives and taxpayer investments, continue to need personal protective equipment and disposable clothing products that meet stringent regulatory requirements.
Fortunately, leading protective-wear manufacturers are integrating the latest technological advancements, materials improvements, and designs to keep workers safe in manufacturing facilities, brownfields, construction, and other industries.