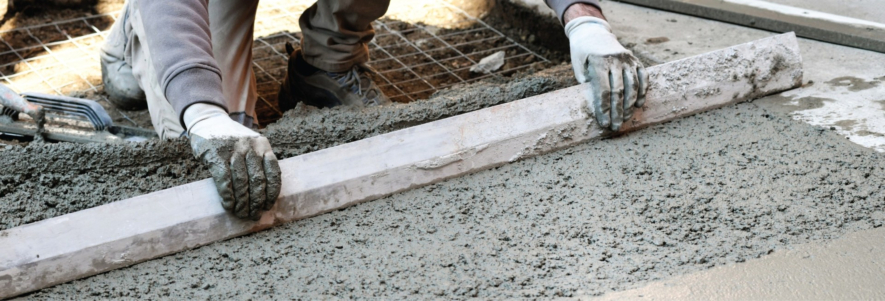
More than 11 million Americans reportedly earn a living in the construction trades, and their efforts can unknowingly expose them to health risks. Although people entering these industries often view heights, tools, and heavy equipment as obvious safety threats, many of the materials used in cement and concrete remain equally dangerous to someone’s health.
One of the materials that may seem relatively harmless at first thought is cement. The powdery material is routinely infused with harsh elements that can burn the skin, damage eyes, or negatively impact the lungs. That’s why construction workers and business owners need to understand OSHA concrete safety precautions and leverage personal protective equipment (PPE) before someone becomes sick or injured.
What is Cement?
It may come as something of a surprise to workers entering the construction trades, but cement and concrete are not necessarily the same material. Cement is typically comprised of materials that may include limestone, chalk, clay, blast furnace slag, silica sand, and iron ore, among others.
Under a controlled process, ingredients are combined and heated to create a rock-like substance called “clinker.” That hardened clinker is then ground into dust that is later mixed with water to form a paste. The cement paste is mixed with other materials to form what we commonly refer to as concrete. In terms of safety precautions for concrete work, it’s essential to understand that the finely ground materials differ between cement types. These include the following.
- Portland Cement: Ranked among the most widely used cements in construction, Ordinary Portland Cement (OPC) leverages materials that include silicates of alumina (clay) and calcium carbonate (limestone and chalk). This general masonry material dominates small project construction.
- White Cement: This variety typically does not include iron oxide, although it remains similar to OPC in other regards. It enjoys limited applications, often determined by its iconic white finish.
- Water Repellent Cement: This fast-hardening material is mixed with metal stearates during the grinding process. Its applications include structures that have ongoing contact with water, such as tanks, swimming pools, and bridges.
- Sulfate Resistant Cement: This slow-hardening material is generally deployed in areas with high sulphate soil content. These often include sewer systems, retaining walls, and coastal piers.
- Rapid Hardening Cement: Containing higher levels of tri-calcium silicate than OPC, this cement product is usually ground to a finer powder. It may be strategically used in construction that demands increased concrete strength in the early stages, such as formwork.
- Expansive Cement: Unlike other materials, this variety tends to expand rather than contract when hardening. Its composition is similar to OPC, but calcium sulfate and sometimes tricalcium aluminate are added to the mixture.
Forming concrete requires a mixture of about 10-5 percent cement with 15-20 percent water to create a paste. That cement-water paste is then combined with aggregates that may include gravel, crushed stone, and sand, among others. In terms of safety, these small dust particles can impact the lungs and prove toxic if inhaled.
Forming concrete requires a mixture of about 10-5 percent cement with 15-20 percent water to create a paste. That cement-water paste is then combined with aggregates that may include gravel, crushed stone, and sand, among others. In terms of safety, these small dust particles can impact the lungs and prove toxic if inhaled.
What Industries Commonly Use Cement?
Understanding the safety precautions for concrete work also includes a separate category of people who handle cement production and usage. This remains an important distinction because wide-reaching construction sector jobs involve pre-mixed concrete. The wet materials pose different health risks than ones associated with manufacturing cement and converting it into usable concrete.
An estimated 90 million metric tons of cement were produced in the U.S. during 2020. That figure represents a steady increase in manufacturing from 67.2 million metric tons in 2010. Those figures indicate year-over-year growth in clinker and cement manufacturing that may expose workers to airborne dust particles and potentially toxic materials.
Adding to their ranks, distribution plants and other large-use facilities require massive amounts of cement to produce concrete on a daily basis. But cement and concrete usage remain pervasive materials used in industries that also include the following.
- Masonry: This construction-sector occupation leverages both pre-made concrete and cement on a routine basis. Stone and bricklaying typically involve a material known as a mason’s tender. This person’s primary responsibility is mixing cement with other elements to form concrete and making it available to masons. This industry also handles pouring and manipulating concrete flooring, retaining walls, and more.
- Infrastructure: Large-scale construction such as highways, bridges, airports, stadiums, parking garages, and sidewalks use concrete for structural integrity.
- Form Work: Contractors and developers generally subcontract foundations and large concrete pours for form work. Form work involves the use of wooden or composite framework that wet concrete is poured into. After the concrete has dried and solidified into the desired shape, the supporting structure is removed using tools such as hammers, chisels, or prybars.
The varieties of brands used to make concrete have wide-reaching health implications. This is largely because dry mixes release dust particles while ready-mixed concrete can splatter on workers.
What are Common Injuries Associated Cement Work?
When considering workplace safety policies and personal protective equipment, business leaders would be well-served to ask and answer a few simple questions.
- Is concrete toxic to humans?
- Is concrete dust dangerous?
The answer to both is: Yes. Wet concrete and the cement base used to create it have hazardous implications for everyday people. For example, workers who pour concrete foundations, slabs, sidewalks, and other hard structures come in direct contact with the material. Splattering concrete can get into the eyes, the ears, or transfer contaminants through skin contact. Some unsuspecting workers can suffer heightened sensitivity to the hazardous materials used in cement, such as lime and chromium. Even seemingly wet concrete harbors trace amounts of crystalline silica that can be inhaled. And when form workers break apart framing, or masons sand and polish concrete floors, the risk of breathing in crystalline silica only escalates.
Dry cement and concrete also pose a greater health and safety risk than new construction workers might realize. It’s not uncommon to bring out heavy equipment to cut deep into concrete slabs or use hand-held power tools to trim cinder blocks and other materials made from concrete. In many ways, those in the masonry professions mirror the way carpenters prepare wooden building materials. But the essential difference is that lumber doesn’t release crystalline silica dust or lime particles into the air.
Manufacturing and construction workers who come in direct contact with cement and concrete often suffer health conditions such as chemical irritation, burns, abrasions, and damaged lungs from intense or prolonged exposure to cement and concrete dust. With the health and wellbeing of employees at risk every time they handle cement and concrete, it’s essential that companies stock a complete inventory of PPE that includes protective clothing.
What PPE is Needed for Working with Cement and Concrete?
Although the cement manufacturing and concrete occupations appear dissimilar, the people doing the work have remarkably similar PPE needs. During both processes, workers must take determined steps to prevent skin contact from finely ground lime, metals, and silica dust, among other hazardous materials. The same holds true of moist concrete that can penetrate the skin, as well as airborne cement dust particles.
- Skin Protection: Frontline workers must leverage full-body PPE such as coveralls to prevent dust particles and splattering concrete from settling on their arms, legs, and torso. Disposable personal protective clothing that can be accessorized with a hood provides enhanced protection.
- Hand Protection: Waterproof and dust-resistant gloves are essential health and safety necessities for cement and concrete handling. Top products eliminate gaps between hand protection and the wrist area.
- Foot Protection: People who work with wet concrete must take significant measures to prevent skin contact inside their footwear. Rubber boots are considered standard safety protections when pouring slabs, floors, and other structures that require wet concrete manipulation. It’s also crucial for cement manufacturers and those tasked with cutting and grinding to use protective footwear coverings whenever practical.
- Lung Protection: An overwhelming number of construction sector occupations face significant lung conditions due to the presence of silica dust. Masks with a high particle filtration efficiency or respirators, depending on the application, rank among the most important accessories for protecting against concrete dust inhalation.
What are OSHA Concrete Safety Guidelines?
The Occupational Safety and Health Administration publishes guidelines that detail the need for best practices and PPE in the cement and concrete sectors. For individuals working with cement and concrete, OSHA indicates employers need to apply regulations regarding manufacturing or construction. These generally require PPE that covers exposed skin, eyes, protects against dust inhalation, and involves footwear.
To comply with OSHA mandates, business owners and decision-makers would be well-served to educate employees about the risks of dust particles in enclosed spaces, proper ergonomics, and the need to replace wet or dust-covered gloves, coveralls, masks, as well as common knee and elbow padding regularly. Companies engaged in cement manufacturing and concrete use are advised to have an ample supply of PPE and disposable protective clothing items available.
If your workers come in contact with cement or concrete during their shifts and need protection, International Enviroguard produces a complete line of certified disposable personal protective clothing that can decrease on-site risks and increase productivity.