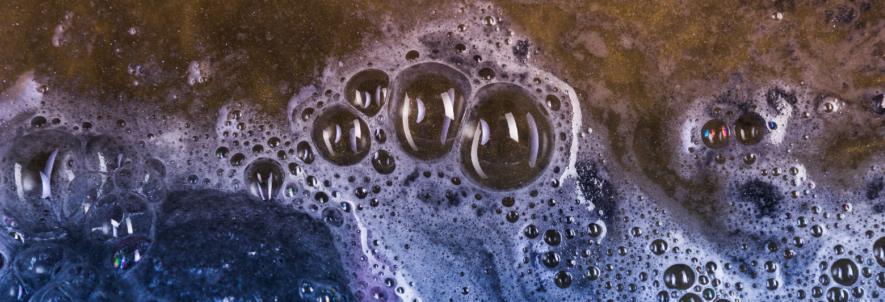
Automotive, medical, and electronic components operations rely on parts washers to eliminate contaminants such as grit, grime, oil, grease, mold spores, and paint from wide-reaching products and materials. Although people operating these devices routinely encounter hazardous materials and toxic cleaning chemicals, parts washing safety protocols are not always followed.
Failing to provide adequate personal protective equipment (PPE) and disposable clothing puts hard-working community members at unnecessary risk. By better understanding their hazard exposure and implementing parts washing safety tips for workers, employers can reduce call-outs, insurance claims and provide an environment that meets safety standards.
What is a Parts Washer?
Parts washers are powerful pieces of equipment used to sanitize items in a fast and efficient manner. Although an increased number of parts washers are considered automated, employees still conduct a variety of tasks, exposing staff members to dangerous chemical agents and fumes.
In many cases, workers are tasked with pre-washing parts before being placed inside these commercial cleansing machines, resulting in liquid toxins splashing their clothing, face, arms, hands, feet, and eyes.
This health and safety vulnerability may stem from the fact that companies purchase parts washers to reduce workplace risks. For instance, an immersion parts washer carries out the cleansing facets internally.
Because of their investment in parts washers, some business professionals anticipate that the dangers of cleaning by hand have been eliminated. Nothing could be further from the truth. Before anyone can safely handle and prepare the parts or set up the cleaning equipment, health and safety risks must be identified.
Conduct a Parts Washing Safety Assessment
While some people think in terms of risk, it’s important to consider assessments as an opportunity to make the workspace safer. People who oversee the parts-washing process may unknowingly encounter hazardous cleaning agents and materials that cling to articles of clothing. The pre-washing process presents a vulnerable point of contact that must be addressed.
These are considerations to include in your Parts Washing Safety Checklist.
- Operational Controls:Workers must be fully trained and educated about how to operate the equipment safely. This may include settings, locking mechanisms, guards, and appropriate procedures. It’s also crucial to check that the equipment is secure and performing properly.
- Solvent Selections: Company policy should mandate that only approved solvents be employed. It’s also essential that workers understand the risks associated with contact and flammability. Consider switching to less toxic solvents, if possible.
- Air Flow: Fumes and diminished air quality put employees in imminent danger. The Occupational Safety and Health Administration (OSHA) mandates that work environments provide free-flowing fresh air. During your safety assessment, consider whether parts washing areas have adequate ventilation and a reliable source of breathable air.
- Ignition Hazards: Many of the intense chemicals used to cleanse parts are flammable. Employers are tasked with posting signage such as “No “Smoking,” as well as establishing a fire hazard safety policy. It only takes one spark to set off a chemical fire.
- Cross Contamination:Commercial parts washing equipment typically serves multiple purposes. When different items require washing, other solvents are generally employed. Before workers transition over, the machinery must be completely cleaned to avoid dangerous chemical mixtures. For instance, peracetic acid and other oxidizers cannot come in contact with water.
- Leakage:At the beginning of each shift and at specified points in the process, safety supervisors would be well-served to check for leaks, tank seal security, and slippery floors. Chemical spill kits should be available, in the event of a leak or a spill of hazardous chemicals.
- Waste Disposal: State and federal agencies have waste disposal regulations in place that address hazardous chemicals and parts-washing debris. Part of the safety assessment includes building these mandates into the company’s practices to ensure compliance.
A parts washing safety checklist must also include removing empty boxes and materials that clutter the workspace. Employers must provide daily access to PPE, disposable protective clothing, and a place to change into safety clothing and equipment without risk of contamination.
Follow PPE Parts Washer Compliance
Following a safety assessment, employers are required to follow OSHA’s General Industry standards when setting up and operating parts washers. Employees should receive advanced and ongoing safety awareness training regarding the pre-cleansing process, equipment operation, hazardous agents, and the vital use of PPE and disposable clothing.
These are applicable safety measures outlined in OSHA’s General Industry rules.
- First-Aid: Workers must be taught proper first-aid methods as they relate to dipping, coating, and parts washer preparation hazards.
- Hygiene:People who utilize hazardous chemicals must have a storage and changing area to prevent street clothes from becoming tainted. A separate locker room or changing area is typically used where employees can undress and dress away from PPE and soiled disposable protective clothing. It is also advisable for employers to provide a place to shower or flush chemical agents off the body. A hot basin and/or wash hose may suffice in some cases.
- Ventilation Requirements: Part of the OSHA ventilation requirements involve reducing vapors coming from dip tanks. Air that poses a health risk to employees or exceeds 25 percent of the lower flammable limit (LFL) cannot be recycled. That means a fresh-air-in system must also be integrated.
Employers in the automotive, medical, and components industries, among others, will need to look beyond OSHA regulations.
- The Automotive Industry Action Group (AIAG) publishes parts cleaning guidelines.
- The Globally Harmonized System of Classification and Labeling helps classify chemical agents using data sheets.
- The Code of Federal Regulations (CFR) issues advisories regarding eye, face, and respiratory safety, training, and parts washer equipment maintenance.
- Electrical hazards and flammable items generally fall under the National Fire Protection Association’s 70E (NFPA).
- Lastly, the International Safety Equipment Association (ISEA) determines which gloves, goggles, face shields and other garments meet the chemical resistance standards for parts washing operations.
Parts Washing Safety Tips for Workers
There are ways that employers can minimize the risk of workplace injuries and ailments for parts washing departments. Exhaust ventilation and fresh air flow do not have to be limited to the OSHA minimum standards.
Increasing the number of breaks and adding industry-leading air filters are other ways to lower the risk of a respiratory condition. Companies can take advantage of next-gen technologies that are helping to automate parts washers and high-volume equipment, which reduces the number of cycles.
At the end of the day, employees need to follow safety measures to the letter, and these parts washing safety tips for workers.
Handling Chemical Agents
Employees should never assume chemicals can be mixed unless expressly stated in the safety data sheets. Otherwise, relatively harmless chemicals can become volatile and dangerous. That’s why cleaning leakage and spillage promptly and thoroughly is crucial.
The harsh chemicals used to strip paint and grease off parts present a significant health and safety risk. Companies would be well-served to provide spill kits to minimize wet floor hazards.
Environmental Safety
Loose debris, empty containers, and puddles are non-starters in parts washing areas. Slip and fall accidents account for upwards of 400,000 workplace injuries annually, according to the Bureau of Labor Statistics.
In 2022, hard-impact falls were responsible for 1 out of every 5 workplace fatalities on construction sites. Not only can staff members in the parts washing area suffer broken bones, concussions, and sprains, but they could also make dangerous contact with commercial-grade cleaning agents.
Wear Disposable Protective Clothing
Standard PPE and disposable clothing include goggles, face shields, and safety clothing that covers the entire body. Chemical splash suits with hoods are needed to prevent skin burns and lesions. Rubber gloves and footwear covering are critical in terms of preventing skin contact or cross-contamination of street clothes. Parts washing staff members must also adorn breathable masks that filter out particle pollutants.
Maintaining an inventory of personal protective disposable clothing is essential to keeping parts washing staff members safe. The PPE and disposable clothing products must be easily accessorized, resist chemical penetration, and demonstrate fire resistance.