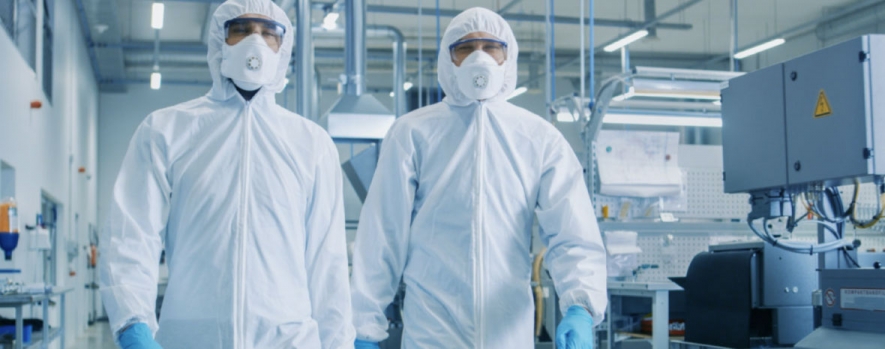
If you have a cleanroom facility, you know the importance of incorporating preventive equipment, devices, and materials to maintain a clean, bacteria-free, and germ-free environment. In the absence of proper gowning techniques and procedures for employees, investing in such equipment defeats their purpose. This because humans are the greatest threat to the sterility of a cleanroom. Although personal protective equipment such as gloves, frocks, hairnets, shoe covers, and coverall suits minimize the risk of contamination, their efficacy is limited without suitable gowning procedures.
Defining a cleanroom
A cleanroom refers to a controlled environment where the introduction, retention, or generation of contaminants such as dust, aerosol particles, microbes, and chemical vapors are kept at a bare minimum. In a cleanroom, other parameters, including humidity, pressure, and temperature, are also controlled. Cleanrooms are a common phenomenon in manufacturing, research, pharmaceutical, medical, and electronic part production facilities. This is because the products manufactured by these industries are sensitive to particulates and could get damaged if they come into contact with contaminants. Upcoming industries, including artificial intelligence (AI) and nanotechnology, also make use of cleanroom conditions. Cleanrooms are classified by the International Standards Organization (ISO) according to the extent of contamination control. The classification is based on the concentration and particle size allowed per volume of air, and range from ISO Class 1 to ISO Class 9. The lower the number, the ‘cleaner’ the cleanroom is.
Maintaining a sterile cleanroom environment
Maintaining a suitable level of cleanliness and sterility in a cleanroom is achieved through two major ways. First, the air that gets into the cleanroom is purified through HEPA (High-Efficiency Particulate Air) filters. Although the level of filtration depends on the level of cleanliness you require, these filters can eliminate contaminants as small as half a micron. Proper gowning techniques is the second way of maintaining cleanliness in a cleanroom environment. This refers to the procedures employees need to go through in readiness for the cleanroom workspace.
Cleanroom gowning procedures
The extent to which employees need to gown up differs depending on the cleanroom class. For instance, in ISO 7 and 8 cleanrooms, frocks are accepted while the same is not recommended in an ISO 4 cleanroom. This guide gives you a brief overview of the gowning techniques you should put in place to minimize particle dispersion and subsequent cleanroom contamination.
Pre-gowning techniques
Once the employees get to the worksite, they should undertake a preliminary cleaning of the exposed parts of the bodies, including the face, hands, and lower arms and remove their regular clothes. Cleaning using approved sanitizing soap helps get rid of skincare products, dirt, and makeup, which could contaminate the cleanroom. Oftentimes, jewelry such as rings, watches, necklaces, and so on need to be removed. Tacky or sticky mats are also a common pre-gowning practice. As the name suggests, this mat has a sticky surface that pulls of dirt and debris from the soles of your employees’ shoes. This helps keep the sterile cleanroom environment free of impurities.
Appropriate gowning practices
This gives you a general overview of some critical steps your employees should go through during the gowning process.
1. Hand washing
Although the order of steps during the gowning process is debatable, the general rule is that hand-washing comes first. Some of the hand-washing practices you should teach your employees to observe include:
- Always use approved cleanroom soaps
- Wet hands with water and apply the soap.
- Scrub your hands to the elbows for at least 15 seconds, taking care to clean under the fingernails
- Paper towels should never be used. Instead, HEPA equipped hand dryers should be installed
- You should never refill soap dispensers
2. Putting on the first pair of gloves
Get into the gowning area without touching the door. Make sure you step on the tacky mat or any other mat provided. Proceed to wear the first pair of gloves after sanitizing your hands with the provided spray or gel. The glove material depends on how reactive the cleanroom environment is. Popular choices of cleanroom gloves include neoprene, latex, vinyl, nitrite, and tri-blend chemical gloves.
3. Top to bottom gowning technique
A suitable gowning procedure should start from top to bottom. This implies that your employees should begin by donning their hoods and end with their shoe covers. This prevents contaminants or particles from falling to already gowned parts. Once you have put on the hood or bouffant cap and face mask, ensure both fit snuggly and that there are no gaps around the mouth and nose.
Most facilities use frocks, coveralls, lab coats, or isolation gowns to conceal street clothing. These garments should not touch the floor during the gowning process. If you are using coveralls, make sure that the lower part is tucked into approved cleanroom boots. Once you are done, put on your cover shoes. If other items such as face masks or goggles are provided, put them on. Sanitize your gloved hands once more before proceeding to put on the second pair of gloves. Once this is done, check yourself in the mirror and if there’s a checklist provide, make sure you conform to all the listed items.
Cleanroom protocols
Some of the protocols that will help you maintain a contaminant-free cleanroom environment include:
- Should any gowning garments tear as your employees dress up, they should begin the process all over again with new clothing. This minimizes the chances of possible contamination.
- Movements increase the risk of cleanroom contamination exponentially. This is because humans emit thousands of particles as they move. Therefore, once your employees get into the cleanroom space, their movement should be minimal or none at all. If they must move, they should do so slowly.
- Cleanroom garments that are too small or too large could increase the risk of contamination. Employees should also be trained on how to seal all the gaps between clothing. This includes tucking hoods into coveralls, sleeves into gloves, and coveralls into boots.
- Employees should not eat in the cleanroom. Tobacco products and chewing gum should also not get into the cleanroom.
- It is a good idea to have a pair of shoes used only in the cleanroom. If they change into this even before getting into the gowning area, there’s a lower chance of contaminants getting tracked into the workspace.
- Discourage your employees from using perfumes and hairsprays that could give off unnecessary fumes, which could endanger your cleanroom’s balance.
- Wipe down any cleanroom tools or supplies using an isopropyl alcohol solution.
Train and retrain your employees to ensure that they are conversant with all the gowning protocols and procedures. Posting reminders just outside the gowning room is an effective way of reminding employees of the acceptable practices. Make sure your employees understand the importance of the appropriate gowning process to the maintenance of your cleanroom’s standards.