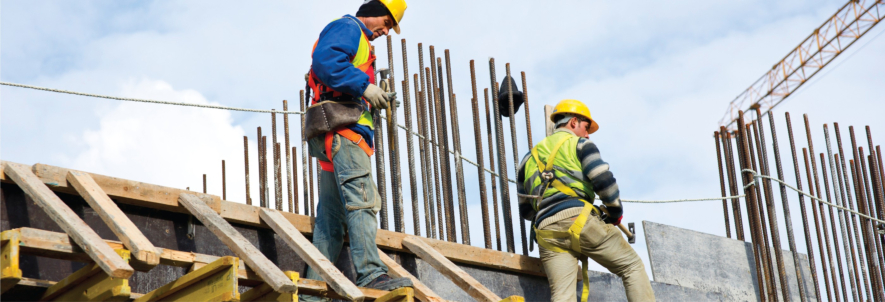
Workplace injuries, illnesses, and fatalities dramatically declined roughly throughout the last half-century due to heightened awareness about construction safety gear. The Occupational Safety and Health Administration (OSHA) created and updated regulations regarding best practices and personal protective equipment (PPE) that resulted in daily workplace fatalities decreasing from 38 in 1970 to 15 in 2019. That 21 percent reduction was also mirrored by construction injuries and illnesses dropping from 10.9 per 100 workers in 1972 to 2.8 in 2019.
While the increased use of construction PPE gear played a significant role in worker health and safety, not all companies have adopted the OSHA PPE standard for construction. Similarly, not everyone has actively educated men and women in the trades about prevalent risk factors or how construction safety gear protects them.
That’s why the Biden Administration is pushing to hire more OSHA inspectors to ensure hard-working construction professionals finish each shift without incident or injury. The goal is to double OSHA’s inspection staff to roughly 1,500 individuals by 2024. New inspectors would likely focus on violations that contribute to the notorious OSHA Focus Four, or Fatal Four in tragic incidents. Construction decision-makers would be well-served to identify and remedy these issues before employees are injured or OSHA levels a hefty fine.
What is OSHA’s Focus Four?
Along with establishing regulations, OSHA compiles statistics to identify and resolve workplace hazards. Over the years, data consistently points to four primary issues that result in workplace fatalities. The so-called Fatal Four involves the following preventable incidents.
- Hard Falls
- Being Struck by an Object
- Electrocution
- Getting Caught Between Equipment.
Some construction businesses refer to workplace injuries and accidents even when OSHA regulations were ignored, or construction PPE gear was not worn. In such cases, OSHA’s Fatal Four are not accidents. The injuries and deaths are the result of negligence. Given that hard impact falls account for one-third of construction fatalities, employers and employees would be wise to resolve the following hazardous situations.
1: Failure to Provide Fall Protections
Under OSHA Regulation 29 CFR 1926.501, fall projections come into play anytime someone is “working or walking” at a height of 6 feet or higher. When elevated to 6 feet or higher with open areas or edges, the impact of a fall can result in significant injury or death. Broken bones, torn soft tissue, or traumatic brain injuries can result when someone lands on debris, rock, or construction equipment. That’s generally why construction PPE gear such as hard hats are required for people on the ground and those working at elevations.
How to Comply with OSHA Fall Protection Rules
People working on rooftops, scaffolding, and buildings that have not been walled-in yet rank among the more prevalent job sites where fatal falls occur. Meeting OSHA regulations in these situations tasks construction companies with providing and insisting workers utilize the following:
- Guardrails: Open-air areas have increased protection when barriers are put in place to prevent falls. OSHA regulations insist that some type of “smooth-surfaced” system be used so that construction PPE gear does not get snagged, or workers suffer lacerations. Guardrails or sturdy guidelines may also be used in these spaces.
- Fall Arrest Protection: The OSHA PPE standard for construction in these instances typically involves a tested and certified harness, deceleration system, lifeline, or anchorage. Like rock-climbing gear, the underlying principle is to slow and stop someone who is falling from making a hard impact with the ground or anything along the way.
- Travel Restraints: Roofers routinely use these systems to prevent them from inadvertently stepping or slipping off the building’s soffit. Many involve a five-point harness connected to a line that is securely anchored. Workers enjoy the mobility to perform jobs at heights without the risk of falling.
It’s important for supervisors to thoroughly inspect fall protection systems before employees begin work. An installation error or safety equipment defect can result in precisely the incident construction professionals are trying to prevent.
2: Faulty Scaffolding
The Bureau of Labor Statistics indicates that more than 60 percent of construction projects use scaffolding, and safety violations are a persistent problem. Many of the scaffolding failures are entirely preventable. But allowing unseasoned or untrained workers to install these temporary structures can lead to errors.
Failure to install a secure scaffold puts unsuspecting users, who were not necessarily involved in its setup, at a high risk of injury. Insufficient scaffolding also puts construction companies in the crosshairs of OSHA Regulation 29 CFR 1926.451. The failure to implement a compliant scaffold places workers at a greater risk of injury and violates OSHA regulations.
How to Comply with OSHA Scaffolding Rules
According to Regulation 29 CFR 1926.451, scaffolds must be “capable of supporting four times the maximum intended load without failure.” In practical applications, these usually involve implementing a “four times” rule. Planks must be rated to manage four-times the anticipated load, and the same holds true for footings. Supervisors must also make sure the staging is properly secured to the building’s façade or in a way that maintains its upright posture regardless of high winds or load shifts. OSHA also tasks construction businesses with having a qualified person oversee scaffolding setup. This individual must be considered “capable of identifying existing and predictable hazards.”
3: Unsupported and Defective Ladders
In terms of the construction sector, ladder violations rank among the top three most cited by OSHA. Ladders are nearly as essential as hammers and circular saws in the construction trades. But the fundamental differences are that too many companies use defective ladders that should be retired, and workers do not receive adequate safety training.
The result of these shortcomings is that employees sometimes feel pressured to climb faulty rungs that give way. At other times, ladders are not securely footed and kick out while someone is working at an elevation. Should more boots-on-the-ground inspectors be hired, construction companies can anticipate a flood of OSHA Violation 1926.1053 citations.
How to Comply with OSHA Ladder Rules
Half the battle can be won by simply decommissioning unstable ladders. Smaller construction businesses that try to save a few dollars by adding supports to cracked or declining products are likely to face hefty fines. It’s more cost-effective, as well as ethical, to replace aging and damaged ladders that do not meet OSHA standards listed on the organization’s website.
The other side of the equation involves safety training. Inexperienced construction workers sometimes secure ladders in unsafe ways. That’s usually because they have not yet experienced shifting and sliding while operating hand-held equipment or swinging a hammer at heights. It’s crucial that experienced construction workers educate newer employees about how to properly anchor a ladder and ask a co-worker for help when feeling unsafe.
4: Failure to Provide Adequate Safety Training
It’s easy to see that many OSHA violations result from a lack of workplace training. Supervisors who are busy overseeing a jobsite too often hand off a new hire to an employee. The expectation that a peer will fully train someone is not always realistic. In construction, team members are expected to demonstrate they are productive, and safety training takes a backseat.
The statistics and anecdotal data accumulated by OSHA since it was formed in 1971 point to lack of training as a primary reason for injury, illness, and workplace fatalities. To reduce these preventable incidents, Regulation 29 CFR 1926.503(a)(1) was crafted. The rule provides employers with guidance and indicates hefty fines when companies do not fully train people. If a worker can anticipate being exposed to heights, hazard training must be completed in advance.
How to Comply with OSHA Training Mandates
Decision-makers would be well served to establish a safety training program covering the OSHA Fatal Four. The program should involve fall issues specific to the projects a business undertakes and teach how the necessary construction PPE gear functions. Instructors often discover that even experienced workers may not know the appropriate construction safety gear to utilize or how to properly secure items such as harnesses.
It’s also important to avoid approaching safety training as if it were a checklist nuisance. On-site instruction and follow-up under live conditions are vital to ensure community members complete their shifts and do not become an OSHA statistic.
What is the OSHA PPE Standard for Construction?
Based on the OSHA General Duty Clause under Regulation OSHA Act Section 5(a)(1), supervisors and company leaders are tasked with ongoing equipment inspections and monitoring practices with safety and injury in mind. Things such as faulty ladders and scaffolding are just as hazardous as not wearing industry-certified construction safety gear.
Personal protective gear for construction generally includes a PPE suit/coverall, as well as gloves, breathable masks, and other accessories like hard hats or high visibility gear. International Enviroguard produces a complete line of personal protective clothing that exceed the OSHA PPE Standard for Construction.