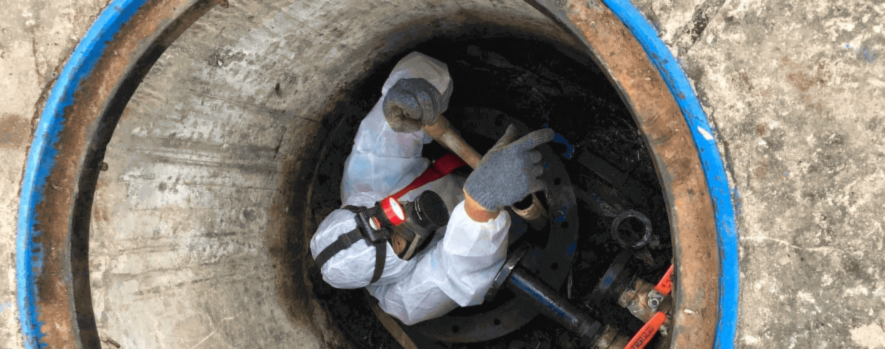
The need for workers to perform tasks in areas that are considered “confined spaces” heightens the risk of injury and fatalities. These spaces are often not designed for humans to complete a job but are large enough for workers to enter. Making things more difficult is the worker is oftentimes wearing PPE or disposable protective clothing. Being in tight quarters limits a person’s ability to enjoy consistent air ventilation or step away from airborne dust and sparking debris. That’s why it’s essential to have the best possible personal protective equipment and take precautions while working in confined spaces.
What Are Confined Spaces?
The Occupational Safety and Health Administration (OSHA) often speaks to a “permit-required confined space.” This term includes areas that may harbor hazardous gases or unsuitable air. Permit-required confined spaces also may house risky materials that can suffocate and worker, as well as angled walls and floors that present significant dangers. These spaces may also expose workers to electrical wiring, machinery, or heat stress. These are examples of permit-required confined spaces OSHA commonly cites.
- Tanks
- Vessels
- Silos
- Storage Bins
- Hoppers
- Vaults
- Pits
- Manholes
- Tunnels
- Equipment Housings
- Ductwork
- Pipelines
Ranked high among the risks that workers take by entering a confined space are skin contact with hazardous chemicals and other liquids, as well as diminished air quality. It’s not uncommon for the atmosphere in a tight space to lack ventilation, and dangers such as methane, carbon monoxide, and hydrogen sulfide may reduce oxygen levels to critical levels.
In open workspaces, a minimum 21-percent oxygen level is required to sustain the human body. When working conduct tasks in an enclosed area, the heat, dust, and other considerations can cause oxygen decline to between 12 and 16 percent. Even the healthiest industry professional may experience an increased heart rate, loss of coordination, and heightened sweating. If the oxygen drops under 10 percent, people often become nauseous or lose consciousness. Before anyone enters or conducts work in a confined space, it’s imperative to complete a risk assessment.
Conduct A Confined Space Risk Assessment
It’s not uncommon for workers to enter areas that put them at risk because they are not identified as confined spaces. Workplace supervisors are not always mindful of the fact that even a space that a worker can reasonably move around in could put them at risk. A confined space does not necessarily mean a person must squeeze into it.
The fact that it lacks sunlight, contiguous airflow, or is difficult to shield a worker from flying debris from tasks such as cutting, grinding, and even shoveling could qualify it as a confined space. Given that OSHA considers a farm silo a confined space, they are clearly larger than some may believe.
That’s why foreman and decision-makers would be wise to conduct an assessment of the area that has the potential to put workers at risk due to confined space attributes. OSHA mandates the following due diligence under industry-standard 29 CFR 1910.146 before entering a permit-required confined space:
Evaluate each space to determine if it is a confined or enclosed space subject to physical or atmospheric hazards such as those described above.
Once identified, mark these spaces and prevent unauthorized entry.
Evaluate the purpose for entry; limit the initial entry to assessment activities only.
Develop and implement an entry program that includes a means of evaluating the hazards of each space; specifying acceptable entry conditions; a system permitting entries; training for entrants, attendants, and supervisors; air monitoring; and provisions for rescue/emergency services.
Eliminate, control, or otherwise protect workers from all hazards identified in the space before entry and document this procedure.
Ensure that the entrant and attendant are able to communicate throughout the entry.
Exit the space immediately if unsafe conditions develop (failure of ventilation system, meter alarms, experience unexplained symptoms).
Emergency rescue must be attempted only by individuals who are trained in safe entry and rescue procedures and who have the proper tools and personal protective equipment, such as self-contained breathing apparatuses for entry into atmospheres that are immediately dangerous to life and health.
Based on planned activities and anticipated hazards, select protective clothing, respiratory protection, gloves, and other PPE.
Conducting a workspace assessment that identifies confined spaces is the first step to providing employees with the vital personal protective equipment and clothing necessary to reduce the risk of injury and harm. With these spaces identified, the hazardous materials and ventilation can be negotiated. Along with equipment to appropriately ventilate these enclosed areas, supervisors will need to have the highest quality personal protective clothing options readily available. But making decisions about these items can be complicated, given the unforeseen hazards in commercial and industrial landscapes.
Selecting Protective Clothing For Confined Spaces
Organizations that conduct work in a commercial and industrial setting are required to provide appropriate personal protective clothing to all employees. The challenge decision-makers often face is the changing risk factors. OSHA, for example, mandates that unique and certified safety equipment be worn to protect against specific hazards. These are OSHA expectations in terms of equipment and personal protective clothing for confined spaces.
Atmospheric Hazards
The workplace safety agency insists that outfits assess the potential risk of toxic agents into the air. These include conducting due diligence on items such as tanks and other equipment that could release chemicals, gases, or potentially flammable compounds into a space. The presence of materials such as asbestos or dust particles also requires enhanced protections that include, “Select protective clothing, respiratory protection, gloves, and other PPE,” according to OSHA.
Physical Hazards
Supervisors are expected to take proactive measures to ensure workers are not injured by falling debris, broken glass, or other physical dangers. Because every risk cannot be purged from the environment, workers are expected to have protective outerwear, gloves, and respirators, among others.
Power Tool Safety
It’s important to keep in mind that it’s not only the workspace that poses a danger. The powerful tools used to cut, drill, and grind hard materials release dust particles and sparks. Skin contact and inhaling these hazards creates a clear and present danger to the workers who use them and others in close proximity. Confined spaces increase health risks from exposure and contact. OSHA requires companies to supply, “Hearing protection for noise, hand protection for cut- and abrasion-control and vibration dampening. Eye protection appropriate to the impact hazard.”
Chemical and Hazardous Material Storage
The dangers of skin, eye, and inhaling of liquid and accompanying gases place workers in harm’s way. Chemical splashes and inhaling could prove fatal without personal protective equipment. OSHA mandates face shields, splash resistant coveralls, disposable boots, respirators, eye protection, and gloves, among others.
Black Water Hazards
It’s not unusual for contaminated water to be trapped inside confined spaces for long periods. Even in spaces that could only potentially house black water, OSHA requires waterproof protective clothing such as coveralls, disposable boots, and gloves, among others.
Organizations that are tasked with purchasing and storing these and other personal protective clothing options and equipment, would be well served to work with a company that can deliver all of your needs.
Why Industry Leaders Choose International Enviroguard Personal Protective Clothing
International Enviroguard designs personal protective clothing that protects workers against the confined space dangers identified by OSHA and other safety organizations. Along with improved comfort and exceeding industry safety standards, utilizing International Enviroguard products means that your workforce will have a single line that seamlessly fits together and ensures safety.