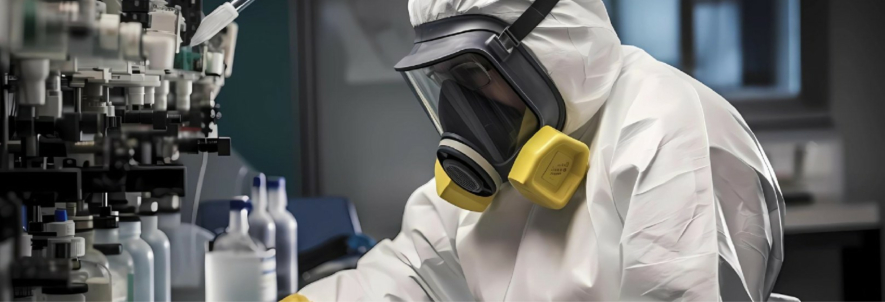
The importance of cleanroom contamination control goes to the heart of whether laboratories can complete sanitary tasks and the ability of manufacturing companies to produce high-functioning products without defects. To maintain these regulated spaces, the potential sources of cleanroom contamination must be identified and addressed as a matter of policy and everyday practice.
Operations typically deploy a mix of standardized equipment and emerging technologies to mitigate the risk of pollutants entering the controlled environment. However, the need for industry-leading sterile clothing for cleanrooms has not necessarily been adequately addressed.
Which Industries Need Cleanrooms?
Companies establish cleanroom contamination control procedures to minimize the possibility of product or process corruption. The strictness of sterilization and decontamination procedures is largely determined by the tasks performed or the vulnerability of materials.
Items such as dust, microbes, vapors, and biohazards must be tamped down to acceptable levels with the right equipment and best practices. These are industries that utilize varying types of cleanrooms.
- Manufacturing Operations
- Laboratories and Research Facilities
- Pharmaceutical Corporations
- Microchip Processing Plants
- Electronic Device Assembly Areas
- Aerospace Organizations
- Nanotechnology Businesses
- Optics and Lens Manufacturing Facilities
- Military and Defense Sector
The individual processes that are conducted within these and other industries usually determine the level of cleanroom contamination control that needs to be maintained. This involves rooting out the sources of cleanroom contamination to meet the required sterility assurance level (SAL).
Why Must Cleanrooms Maintain Certain Sterility Levels?
It’s important to understand that no room can be completely free of contaminants. With that fact in mind, the goal of people who operate cleanrooms is to meet appropriate industry standards called the “Sterility Assurance Level,” or SAL.
An SAL essentially defines the level of cleanliness a product or process needs based on the protocols used by the operation. The SAL is typically articulated in technical terms such as 10-n. Sterilization measures are usually represented by asserting metric examples such as 10-3 or 10-6.
This generally correlates to the number of pollutant particles per cubic meter in a given space. Technical jargon aside, lower SAL values indicate better rates of cleanroom sterilization. Some quality control professionals simply assign an SAL grade to specific areas along the following lines.
- Grade A; Equivalent to an ISO 5 Cleanroom Environment at rest and in operation: At this level, cleanroom contamination control policies rank among the most stringent. This level is the “cleanest” and performs sterile operations. Used for high-risk operations that require heightened sterility, sources of cleanroom contamination must be minimized to allow safe processes such as stopper bowls, filling zones, open ampules and vials, and aseptic processes. A Grade A rating means the cleanroom maintains the highest standards and among the highest possible SAL.
- Grade B; Equivalent to an ISO 5 Cleanroom at rest and an ISO 7 Cleanroom in operation: A Grade B cleanroom typically serves as the background space for Grade A operations. This may involve filling processes and aseptic preparations. Although considered semi-critical tasks, they must achieve a higher SAL to support Grade A cleanroom processes. In lay terms, they must be spotless and largely contaminate-free.
- Grade C; Equivalent to an ISO 7 Cleanroom at rest and an ISO 8 Cleanroom in operation: Often used to perform non-critical manufacturing tasks, Grade C cleanrooms cannot introduce foreign agents that would undermine a product’s integrity. For instance, workers tracking dust or debris clinging to their clothing could impact items during the pre-packaging or distribution phase. That’s why sterile clothing for cleanrooms at this level remains an essential practice. This grade often includes tasks such as preparation of solutions to be filtered and component handling.
- Grade D; Equivalent to an ISO 8 Cleanroom at rest, not defined for “in operation”: To a lesser degree, people working in Grade D environments must also avoid introducing contaminants to the manufacturing process. Much like Grade C, this grade also carries out less critical manufacturing tasks such as handling components after washing and plasma stripping.
Regardless of how organizations decide to rate their workspaces, meeting the proper SAL threshold assures they can safely conduct specific tasks or produce specialized products at acceptable industry standards. The challenge operations face is identifying sources of cleanroom contamination that sometimes go unnoticed.
What are the Top Sources of Cleanroom Contamination?
Effective cleanroom contamination control tasks policymakers with identifying sources specific to their industry and environment. There are more moving parts than some realize until a quality control professional looks closely. These rank among the primary ways that pollutants enter otherwise sterile environments.
Human Contamination
Even people who take great pride in their personal hygiene can introduce contaminants into a cleanroom. Brushing hair, scratching an itch, or simply rubbing tired eyes release multitudes of skin and hair follicles. Body lotions, makeup, hair products, and ordinary soaps may also rub off when workers touch surfaces within a cleanroom. Add a non-infectious cough or sneeze, and the integrity of products such as semiconductors can be compromised.
Cleanroom Supplies
Every person and item that enters the cleanroom or its support spaces must be thoroughly vetted. Stockrooms and the inventories housed in them too often fly under the radar. Many of these supplies are considered sterile when they are unpacked and placed in seemingly secure areas. But when multiple people have access to storage areas, cross-contamination becomes a genuine possibility. Add inconsistent temperatures and humidity to the mix, and cleanroom supplies can develop microscopic mold and fungal growths. The result could require a cleanroom shutdown and comprehensive cleanup.
Liquids and Moisture
Creating and maintaining a space with dry air requires critical HVAC systems and enterprise-level filtration. That’s because water, liquids, and vapors can quickly cause bacteria growth. Along with precision air quality systems, policies usually prohibit employees from bringing water and other beverages into Grade A or B cleanrooms.
Labels and Tapes
Ranked among the more overlooked potential contaminants, labels and tapes introduce paper and adhesives into the clean environment. Along with clinging debris, the adhesive portion of these products can leave a sticky residue that later collects dust and airborne debris. To avoid these sources of cleanroom contamination, organizations are advised to invest in certified products.
Personal Protective Clothing
Personal protective clothing is designed to insulate workers from environmental hazards. That does not necessarily mean all garments are created to work both ways. Failings such as loose strings, lint accumulations, and frayed cuffs can pick up or release unclean agents that impact the sterility of the space. The best cleanroom policies leverage disposable/single-use and low-linting personal protective clothing to ensure quality control.
Ways to Keep Contaminants at Bay?
Maintaining the integrity of the cleanroom environment calls for the use of advanced technology and ongoing vigilance. Below are pragmatic ways for companies to reduce or eliminate sources of cleanroom contamination.
- HEPA Filters: Certified filters extract minute airborne particles and keep breathable air clean. The filters require regularly scheduled replacement, and the HVAC systems must be appropriately maintained— Cleanrooms require a specific number of HEPA filtered air changes per hour to maintain the necessary SAL.
- Air Quality Monitoring: Technologies that can accurately measure airborne pollutants help companies regulate air quality and can alert if additional filtered air changes per hour are needed.
- Moisture Management: Maintaining dry air helps prevent bacteria and mold growth. This process must also account for ways to capture human perspiration.
- Decontamination Chambers: Environments that call for the highest sterilization rates typically require secondary spaces for decontamination. They may involve private areas to perform personal hygiene, shower, and change in and out of disposable personal protective clothing.
Along with a decontamination chamber, it’s essential to implement donning and doffing policies for sterile clothing. This starts with providing spaces to strip off street clothes and don disposable protective clothing in a separate room. This practice avoids the possibility of cross-contamination from elements on street clothes. Without a donning and doffing policy, sterile clothing for cleanrooms may be rendered ineffective.
Investing in Sterile Clothing for Cleanrooms
The use of disposable personal protective clothing is crucial to maintaining cleanroom integrity. Industry-leading products typically involve protective head and face coverings, coveralls with hoods, goggles, face shields, and breathable masks. These protective clothing items are usually accessorized with gloves that eliminate gaps at the wrist and footwear coverings.
Diligent quality control professionals generally stockpile a single source of sterile clothing for cleanrooms that can be seamlessly accessorized as needed. International Enviroguard manufactures and distributes a complete line of disposable protective clothing and accessories that exceed cleanroom industry standards.