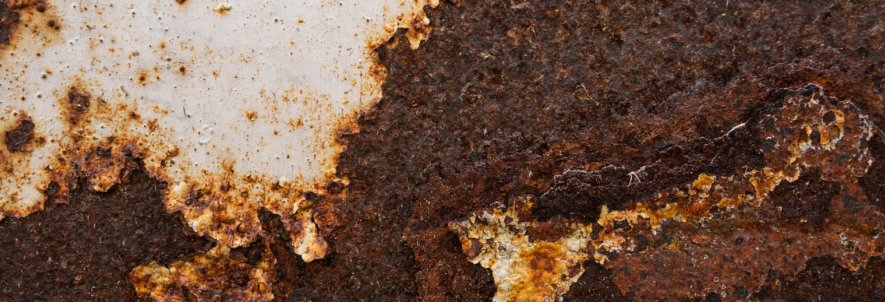
Heavy-duty commercial equipment remains a vital part of the construction, freight transportation, and other industries. Without massive cranes to offload cargo vessels, bulldozers, backhoes, and road graders, the world as we know it would be dramatically altered.
While these large iron and steel pieces of machinery appear almost indomitable, corrosion can negatively impact their structural integrity, putting workers and the environment at risk. That’s largely why the regulatory bodies mandate strict safety and maintenance practices to prevent the corrosion of heavy equipment and keep workers out of harm’s way.
To accomplish these and other goals, it’s mission-critical for organizations to craft and implement a detailed corrosion control policy. Having a system in place to deliver proactive solutions is how to prevent heavy machinery corrosion, protect the environment, and keep hard-working people from suffering avoidable injuries or fatalities.
What is Corrosion and How Does it Occur?
A straightforward way to define corrosion speaks to a slow deterioration of iron, steel, and other metallic components. The naturally occurring process involves factors such as high temperatures, moisture in the air, chemical exposure, and sometimes salt. Anyone who lives near an ocean or the Gulf of Mexico understands that automobiles, trucks, and even outdoor patio grills degrade quickly due to humidity infused with sea salt.
It’s also important to note that corrosion helps return metals to their former oxidized states. Before ores were culled from the Earth and forged into iron and steel for heavy machinery, they did not have hardened integrity. Corrosion essentially reverses the process by creating an oxidation-reduction reaction (redox) on the surface of the metal.
Unfortunately, corrosion is not a favorable natural cycle because it can result in financial losses, pollution, injuries, and even workplace fatalities. When a large piece of machinery falters due to corroded parts, hard-working people suffer.
What are the Effects of Corrosion?
In terms of the impact it has on the economy, estimates show global gross domestic product losses north of $2.5 trillion annually. That figure averages about 3.4 percent per country, depending on environmental factors and regulatory compliance. Studies also indicate that the U.S. suffers the second-highest rate of industrial losses due to corrosion, behind the EU.
These rank among the many tragic accidents related to corrosion.
- Silver Bridge Collapse (1967): An Interstate 35 bridge between Point Pleasant, West Virginia, and Kanauga, Ohio, plunged into the Ohio River after corrosion weakened its structural integrity. The incident resulted in 46 deaths in 1967.
- Sinking of the MV Erika (1999): The vessel literally snapped in two while transporting 30,000 tons of fuel oil. Salt air oxidation had eaten away at the main deck coaming, which is designed to prevent water from flooding a ship. Corrosion also affected the ship’s gas system risers as upwards of 19,800 tons of fuel oil spilled off the coast of France, killing sea life and causing wide-reaching environmental damage.
- Ohio Fair Tragedy (2017): A pendulum-styled fair ride failed due to excessive rust and corrosion that affected the thickness of a beam. The avoidable malfunction killed one person and left others severely injured.
One of the most dramatic corrosion-related incidents occurred in 2023 when a crane collapsed in the Manhattan borough of New York City. Positioned 45 stories high on 10th Avenue, the crane reportedly caught fire after a hydraulic leak struck hot metal. The 180-foot boom collapsed while hoisting 16 tons of concrete high above the area known as Hell’s Kitchen.
The boom slammed into a building on the other side of the busy street before crashing to the ground. A dozen people sustained injuries as the broken wreckage hit the street, along with shards of glass and metal. Extinguishing the blaze and securing safety required upwards of 200 first responders.
How to Prevent Heavy Machinery Corrosion
Although it may not necessarily be feasible to entirely stop corrosion from occurring, there are a variety of control measures that can mitigate its impact on heavy machinery. Adopting proactive measures to reduce and control corrosion can save companies up to 35 percent of what it would take to repair and replace machinery.
These rank among the best practices companies employ in their corrosion management policies to minimize risk and save money.
- Routine Inspections: It’s essential to have a safety professional conduct regularly scheduled inspections to identify outdated parts and search for signs of corrosion. By addressing rust spots early, they can be cleaned and serviced before components begin to leak or lose their tensile strength.
- Predictive Maintenance: Advanced technologies involving artificial intelligence (AI) and Internet of Things (IoT) devices, such as sensors, can remove much of the guesswork from preventative maintenance. These and other innovations can provide predictive analytics that accurately calculate corrosion rates. In practical terms, AI and IoT can alert safety professionals and maintenance teams to address corrosion before it becomes problematic.
- Cleaning Schedules: Equipment and machinery require basic maintenance and upkeep to function at a high level. By making rust abatement part of the cleaning policy, corrosion can be scraped, sanded, oiled, or coated before it becomes a significant issue. Cleaning and maintenance crew members must also wear appropriate personal protective equipment and disposable clothing when using brushes, oils, detergents, and other items.
- Dry Storage: Leaving heavy-duty commercial vehicles and machinery outdoors exposes them to high levels of heat, moisture, and salt in some areas. It may be worthwhile to invest in indoor storage facilities such as metal buildings.
- Protective Coatings: The undercoating products that treat cars, trucks, and SUVs in northern states that salt roads during winter also have commercial applications. Corrosion-resistant paint and other products can shield metal from oxidation.
Lubricants rank among the more efficient ways to insulate metal from exposure. Not only can an oil and lubrication policy minimize corrosion-related mechanical failures, but it can also ensure equipment operates at optimal capacity.
How to Prevent Heavy Machinery Corrosion: Adopt International Standards
To say the creation and adoption of international corrosion standards has made a significant difference would be an understatement. Globally recognized standards for industrial and commercial machinery provide a framework that drives consistency and workplace safety.
These are examples of International Organization for Standardization (ISO) guidelines that apply to heavy-duty commercial and industrial machinery.
- ISO 8502: This international guideline addresses the manner in which metal surfaces must be prepped before corrosion inhibitors are applied. It provides definition regarding the processes required for surface cleanliness and dust mitigation.
Although it has been widely adopted when dealing with cranes and metal infrastructure, it may equally serve as a reasonable guide for construction equipment and other commercial assets. It’s prudent to review ISO and OSHA mandates related to personal protective equipment and disposable clothing inventories when dealing with airborne dust and fibers. - ISO 12944: This guidance involves protective coatings such as corrosion-resistant paints that are commonly used to shield steel from the elements. The ISO standard also goes into great detail regarding application methods and ways to standardize the process. It’s also important to remember that workers who apply paint and coatings must wear appropriate personal protective equipment such as respirators and disposable safety clothing.
Integrating a corrosion-mitigation policy ranks among the most proactive measures available to minimize repairs, machinery replacement, and protect the environment and people from catastrophic incidents.
It may be difficult to fathom that a failure to catch a corroding hydraulic line or coupling could result in a 180-foot crane boom crashing across a New York City street or a tanker splitting in two, dumping thousands of tons of oil in the ocean. These are the outcomes companies may create by not following through on a policy to prevent corrosion of heavy machinery.
Along with a standardized company policy to identify and mitigate corrosion, safety supervisors would be well-served to maintain a complete inventory of personal protective disposable clothing.