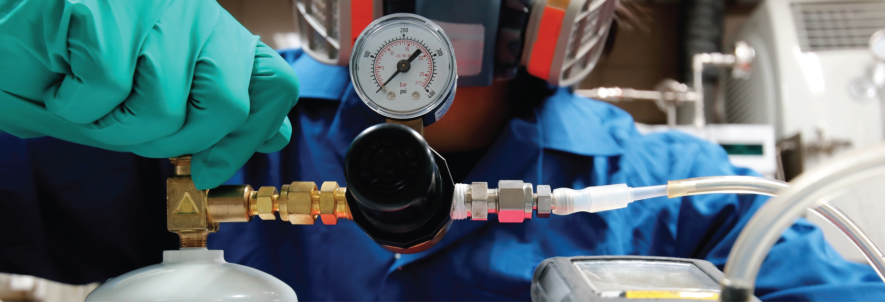
Some work environments come with specific hazards that can affect workers' health and safety. One such hazard can be toxic or poisonous gases, such as chlorine or carbon monoxide. Since these gases are not always immediately detectable, job sites should use a direct-reading portable gas monitor (DRPGM) or other devices to warn employees of any danger.
However, you can't wait until there's a gas leak to know whether your monitor is working correctly. That's where calibration gases come in. This article will break down the ins and outs of calibration gases and monitors, and how to use them effectively on the job.
What is a Calibration Gas?
To understand calibration gases, you have to know how a gas monitor works. These devices scan the air to detect concentrations of a specific substance (like carbon monoxide). Each monitor is set to a particular level, such as 10 parts per million. The level depends on the toxicity of the gas because some are more hazardous than others.
A calibration gas is not just the gas itself. Instead, it's a mixture of gas and air based on the detector's minimum setting. So, if the device needs to be calibrated to 10 parts per million, the calibration gas will match that mixture. These gas/air blends come in canisters that can be hooked up to a monitoring device.
What are Calibration Gases Used For?
Because toxic gases can be deadly, workers should calibrate their detectors at the start of every shift. Calibration gases should be used to calibrate these monitors as often as necessary to ensure everyone's health and safety. Fortunately, modern sensors can auto-calibrate using calibration gases, meaning that workers don't have to adjust anything manually.
What Types of Calibration Gases are There?
All calibration gases can be broken down into two types: reactive and non-reactive. Let's take a closer look at how each type works.
Reactive Calibration Gas
As the name suggests, reactive calibration gases react more to environmental variables, such as heat, moisture, and other elements in the air. Because these gases are more volatile, they have to be treated and stored differently to ensure that they stay stable until used. Typically, reactive calibration gases have a much shorter shelf life of around eight to 12 months.
Some examples of reactive gases include sulfur dioxide, ammonia, and chlorine.
Non-Reactive Calibration Gas
Non-reactive calibration gases don't interact with environmental elements as significantly, and they have a much longer shelf life. While reactive gases are stored in aluminum containers, non-reactive products are stored in steel and often last about three years.
Examples of non-reactive calibration gases include carbon monoxide (and dioxide), alkene, and methane.
Best Practices for Calibration Gases
All employers are legally required to maintain safe environments for all workers, meaning they have to follow best practice guidelines for calibration gases and sensors. The best option is to follow OSHA gas monitor calibration requirements. Here is an overview of some policies to implement on the job.
- Training- Ensure that all workers and supervisors are trained on handling and storing calibration gases. They should also be trained on how to hook up the gas canisters to the detectors to avoid leaks or damaged connections.
- Calibration Drift- Whenever possible, detection monitors should be calibrated in environments identical to those found in the field. For example, calibrating a sensor in a lab setting is far different from doing so in a hot and humid climate. Environmental factors can affect these machines, leading to "calibration drift." Failure to account for this drift can lead to faulty readings and unsafe workplace conditions.
- Expiration Dates- As we mentioned, reactive and non-reactive calibration gases have varying expiration dates. Once a gas has reached that date, it can no longer calibrate effectively. Workers should pay attention to expiration dates and rotate canisters based on a first-in, first-out (FIFO) system.
- Manufacturer Requirements- Gas detection monitors are built to various specifications. Workers should follow all gas detector calibration requirements to ensure accurate readings. If employees don't follow these guidelines, the machines may not calibrate correctly, or the internal mechanisms could get damaged.
- Monitor Protection and Replacement- Gas detection monitors are often exposed to harsh environments and workplace conditions. To ensure that a monitor stays working, employees should try to protect it from drops, hits, and other wear and tear. If a monitor does get damaged, it must be replaced as soon as possible.
FAQs About Calibration Gases
What is a Direct Reading Portable Gas Monitor (DRPGM)?
A DRPGM is a portable device that can detect high concentrations of toxic gases. These monitors can also detect low-oxygen and highly combustible environments. These monitors alert workers with warning alarms if gas concentrations get too high or oxygen levels get too low.
Do Gases Expire? What Happens If a Gas Does Expire?
Yes, calibration gases can expire by either dissipating out of the canister or reacting with environmental conditions. When that happens, the gas/air mixture changes and no longer meets the calibration standards. So, even if there is some gas inside the container, it won't create an accurate reading on the monitor. For example, if the concentration was 10 parts per million, it may have decreased to four or five parts per million.
What is a Bump Test?
A bump test is designed to see whether the alarm systems on a monitor are working. During the test, you release concentrated gas near the detector to see if it will trigger a warning. If nothing happens, the device may be broken or damaged.
What is a Full Calibration?
Generally, bump tests can work well in the field to determine whether a monitor is working effectively. If a device fails a bump test, you should conduct a full calibration to see if it's damaged or broken. A full calibration means using calibrated gas to determine if the sensors are working correctly.
With a bump test, you can release small concentrations of pure gas next to the monitor. For full calibration, only certified calibration gases should be used to ensure accuracy and precision.
What is Calibration Drift and What Causes It?
While it would be great for all gas monitors to work correctly forever, the fact is that sensors and internal instruments can degrade over time. When this happens, the measurements become inaccurate. For example, if a monitor is supposed to detect chlorine at 20 parts per million and starts noticing it at 15 parts per million, the five-point difference is its "calibration drift."
This drift occurs for several reasons, including:
- Natural Degradation- The more a product is used, the more it wears down.
- Disuse- If you haven't used a monitor in a while, it has likely drifted at least a few points.
- Abuse- Drops and bumps can dislodge internal instruments and potentially damage them, meaning that they won't provide accurate readings.
- Environmental Factors- Heat, moisture, and the presence of other gases can affect monitor detection.
How Should Calibration Gases Be Stored?
As we mentioned, reactive gases can be affected by environmental factors more than non-reactive gases, so they should be stored and handled with more care. Here are some general guidelines on how to store calibration gases effectively.
- Keep Out of High-Traffic Areas- Storing them out of the way can prevent bumps and kicks from workers.
- Store in Climate-Controlled Rooms- Heat and humidity can affect the gas, so make sure that they're stored in a cool, dry place.
- Use Manufacturer-Recommended Canisters- Don't try to create your own calibration gases in uncertified canisters. Doing so can lead to inaccurate readings that expose workers to dangerous levels of gases.
How Often Do Gas Monitors Need to Be Calibrated?
Ideally, gas monitors should be calibrated every time workers may be exposed to toxic gases on the job. If that happens every shift, the monitor should be calibrated at the beginning of each new shift. In some cases, once per day may suffice, but you need to make sure that calibration occurs as regularly as necessary. Otherwise, as drift occurs, it could lead to hazardous situations where workers operate in unsafe gas concentrations for too long.
Buy Your Personal Protective Equipment from International Enviroguard
While gas monitors can help protect workers, they're only one piece of the safety puzzle. If there is a hazardous gas leak, workers may not be able to get out of the area quickly. In that case, they need high-quality personal protective equipment from International Enviroguard. Not only will the right PPE protect workers, but it will also allow them to stay safe when handling hazardous materials and gases. Accidents can happen at any time, and you need to be prepared. Browse our extensive PPE collection today and contact us to place your first order.