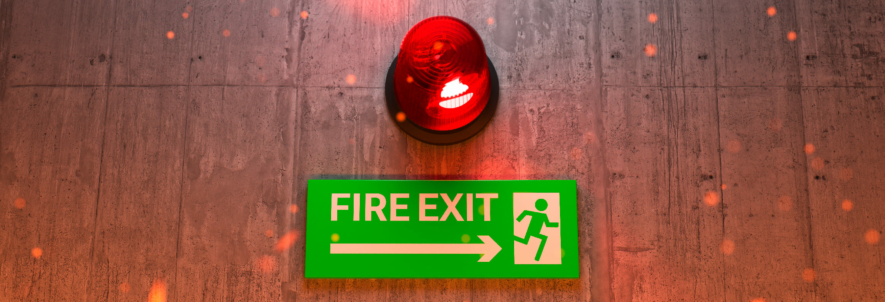
It appears manufacturers need to implement more stringent and consistent arc flash safety methods in the workplace. According to a National Fire Protection Association (NFPA) report, 5 to 10 arc flash incidents occur daily, and thousands of workers are treated at emergency burn centers annually.
These debilitating and sometimes fatal workplace injuries continue to impact electrical teams and peripheral employees despite the NFPA and Canadian Standards Association always requiring strict arc flash safety protocols on the job. Along with ensuring staff members wear arc flash safety clothing, both agencies task employers with crafting an electrical preventative maintenance program that details best practices and enforces them.
What is an Arc Flash & How Does it Happen?
Arc flash injuries typically involve a massive blast of energy, generating enough of a burst to reach thousands of degrees Fahrenheit. Also known as a “flash over,” intense temperatures can sear human skin several feet away and ignite street clothes. Those are the primary reasons why arc flash safety clothing is an absolute necessity.
Along with extreme temperatures, the phenomenon may include a pressure wave powerful enough to knock workers to the ground. During a blast, it’s not uncommon for people in the area to get struck by flying debris, inhale toxic smoke, and require shrapnel removal from unprotected eyes. In terms of workplace accidents, an arc flash event is like setting off a firebomb.
One of the ways manufacturers are reducing the risk of arc flash safety failures is by integrating technology that helps monitor and track electrically driven machines and components. Manufacturers who onboard next-gen devices to improve energy efficiency and streamline inspections are earning the recognition as a “smart workplace.” They also significantly reduce the risk of arc flash injuries and deaths.
What is an Electrical Maintenance Safety Device (EMSD)?
The use of Electrical Maintenance Safety Device (EMSD) products continues to trend in manufacturing and other sectors. Decision-makers often recognize that EMSDs reduce the cost and downtime that come with routine equipment inspections. Leveraging an EMSD program is a positive alternative to the cost-saving practices of delaying inspection for short-term productivity gains. Of course, this short-sighted approach inherently increases arc flash safety risks to electrical crews, inspectors, and the facility at large.
Going the EMSD route allows certified electrical inspectors to forego the need to remove panels, doors, and other protective barriers. And rather than exposing employees to a potential burst of heat, energy compartments can remain intact. Devices are used to test energy consistency and identify any anomalies that may require repair or parts replacement. Although inspectors are still required to wear personal protective equipment and arc flash safety clothing during the process, they face negligible danger.
What Tasks Do EMSDs Perform to Eliminate Potential Arc Flashes?
Various EMSDs are available to manufacturing plants that support arc flash safety methods, help expedite inspections, and provide ongoing monitoring. These devices can offer benefits akin to machine learning by recognizing systemic failure patterns and identifying emerging problems.
Essentially, EMSDs help organizations evolve from the break-and-fix model to taking proactive measures that also improve arc flash safety. The tasks EMSDs help inspectors and other personnel perform may eliminate the need for close exposure to high-voltage energy.
One of the commonly performed inspections conducted under load involves infrared scanning. Unfortunately, too many of the infrared cameras used in manufacturing lack the ability to penetrate safety glass and hard plastics used for viewing access.
There are now specialized EMSD lenses available that allow inspection devices to see through infrared windows and doors. This allows workers to assess components while under load from beyond the potential arc flash radius. Below lists other standard tasks where EMSDs are being integrated.
- Airborne Ultrasound: Ultrasound port technology uses sound waves to identify and assess elements in the immediate air.
- Voltage Detection: External voltage ports allow task-qualified workers to perform verification procedures from the exterior of an electrical enclosure.
- Motor Current Analysis: Voltage tap off connections help determine the operating condition of motors. The EMSD tap off connections help certified technicians to make incremental adjustments.
- Temperature Measurement: While contact processes remain in place, non-contact temperature measurement processes are a critical arc safety method.
- Vibration Analysis: Rotating machinery, such as generators, give off vibrations that can be tracked and monitored for changes. Unusual shuddering can be a telltale sign of a failing asset.
- Power Quality: The Internet-based and fixed data collections serve as early warning systems. Power surges and so-called “dirty electricity” negatively affect machinery and can be monitored.
- Partial Discharge: Addressing partial energy releases early on can reduce the failure rates of generators and other machinery. The ability to locate partial discharges in the beginning phases also reduces workplace risks.
Companies are employing infrared windows and online monitoring systems that provide safety specialists with real-time data. The use of wireless sensors and other Internet of Things (IoT) technologies are also proving game-changing arc flash safety methods.
Building a comprehensive EMSD program that takes full advantage of next-generation technology, IoT devices, personal protective arc flash safety clothing, and equipment better insulates employees from workplace injuries and fatalities.
What is an EMSD program?
The NFPA and Canadian Standards Association provide guidelines for establishing an effective Electrical Preventative Maintenance program, and EMSDs are at the heart of company policies. In manufacturing facilities that use substantial amounts of electricity, arc flashes and electrocutions are top hazards.
Using EMSDs allows inspectors to perform tasks at a safe distance or online assessments with the following benefits:
- Risk Mitigation: Fewer close contact incidents with high voltage and machinery under load provide the physical distance necessary to avoid arc flash dangers and hard impact falls from energy blasts.
- Switchgear Controls: An EDSM program allows inspectors to maintain each switchgear in an enclosed area.
- Cost Efficiency: The ability to conduct online systems checks streamlines the process. Inspections do not necessarily require employees to assess power sources and machinery physically. This means specialists can invest their time and energy in profit-driving endeavors.
- Fire Prevention: Arc flash safety discussions tend to focus on workplace injuries and fatalities. However, high temperatures and arc bursts can result in plant fires. An EDSM program helps reduce the risk of a blaze with early detection.
It’s also important to keep in mind that manufacturers are tasked with meeting stringent workplace safety regulations. The Occupational Safety and Health Administration (OSHA) insists on companies meeting the arc flash safety guidelines outlined by the NFPA. OSHA also mandates that organizations utilize arc flash safety clothing and protective equipment detailed in its Protection From Flames and Electric Arcs rules.
Safety Tips for Reducing Arc Flashes Caused by Electrical Equipment
Taking proactive arc flash safety methods helps significantly reduce the risk of burns, hard falls, and electrocutions in manufacturing plants. When electricians and inspectors are put at risk, arc flashes can result in toxic airborne particles being inhaled throughout the facility, explosions, and fires. Below are arc flash safety methods that help protect everyone.
- Power Down Equipment: Anytime an inspector or electrician needs to make minor repairs or close assessments, safety dictates powering down equipment.
- Ensure Systems Function Property: It’s mission-critical to carry out comprehensive arc flash safety assessment on systems. Complete system assessments can be conducted on a scheduled basis, while problem areas and those that undergo repairs and replacements require more frequent checks.
- Safe Distance: Company safety manuals can set safe distances for electrical assessments. They can also establish best practices when close contact is necessary.
It’s also important to only allow certified, trained technicians to approach high-energy equipment and machinery. When doing so, every team member must always wear arc flash safety clothing and personal protective equipment.