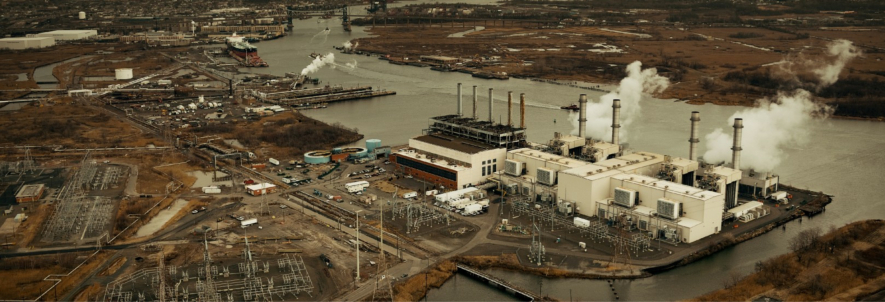
Chemical plants and refineries shut down for routine maintenance, inspections, repairs, and system changes typically on a yearly basis. When shutdown startup safety measures are strictly followed, corporations minimize the risk of injuries, fatalities, environmental harm, and maximize equipment longevity. Unfortunately, human error, equipment malfunctions, and corporate cutbacks have resulted in accidents.
In 2010, research indicated that nearly 50 percent of safety incidents occurred during startup shutdown (SU/SD) processes. The dangers involved in batch processing, catalyst regeneration, product changeovers, and system optimization require industry leaders and supervisors to identify and reduce SU/SD risks.
What are SU/SD Risks?
It’s important for safety supervisors to understand that general plant personnel deal with SU/SD changeovers infrequently. Most of the time, plant workers focus almost exclusively on equipment, technologies, and processes designed for productivity.
Chemical plant and oil refinery stoppages are therefore more of an anomaly. That’s why experienced supervisors are tasked with ensuring shutdown startup safety measures are followed and equipment functions correctly. These are SU/SD risks that too often result in workplace injuries, loss of life, and environmental disasters.
- Safety Hazards: The inherent nature of SU/SD practices has the potential to expose workers to hazardous chemicals, high-temperature splatters, and noxious vapors. Plant and refinery personnel must adorn appropriate PPE and disposable protective clothing due to heightened SU/SD risks.
- Process Disruption: Equipment changeovers and powering up underused assets invites higher rates of failures, leaks, pressure spikes, and dangerous operating abnormalities.
- Environmental Risks: Workers are tasked with the cleanup, handling, storing, and discarding of hazardous chemicals following plant restarts. These environmental contaminants may leak and spill during planned shutdown startup events. When they become airborne, both the environment and workers are exposed to significant risk.
- Equipment Malfunctions: The frequency of changeovers generally increases SU/SD risks due to equipment stress. Inadequate maintenance and poor inspections can lead to unrecognized malfunctions and loss of structural integrity, which negatively affects safety in refinery shutdown startup operations.
- Placing Cost-Effectiveness over Safety: Another SU/SD risk involves companies trying to reduce downtime losses. In some cases, budget cuts reduce the number of experienced safety managers and personnel needed for a seamless systems restart.
- Plant Agility: Plants and refineries that require ongoing startups and shutdowns may struggle to maintain profitable production levels. It’s crucial that plant managers and supervisors are shielded from cost-driven pressures to speed up the process by avoiding non-essential shutdown startup safety measures.
The greatest SU/SD risks are typically the result of human error. Whether this involves a lack of clear, concise communication regarding processes, equipment monitoring, following protocol, or inexperience; people are inherently likely to trigger a sometimes-fatal chain of events.
Adding to the human factor is the fact that oil refineries and chemical plants experience ordinary workforce attrition rates, and new hires may not necessarily receive the hands-on training to ensure plant and refinery shutdown startup safety.
Examples of Failures Due to SU/SD Service
Chemical plant and refinery incidents continue to go under-reported by the mainstream media. As a result, there is less awareness surrounding SU/SD risks regarding fatalities, hazardous material exposure, and environmental impact. Recent reports indicate there were upwards of 829 hazardous chemical incidents documented from January 2021 through Oct. 15, 2023.
During the Texas deep freeze in February 2021, which surprised plant safety operators, chemical spills and leaks made headlines. The same holds true of the recent Norfolk Southern railroad derailment that spilled hazardous chemicals near East Palestine, Ohio. All told, there are nearly 12,000 U.S. facilities that deal with dangerous chemicals, and more than 150 incidents have resulted in 43 deaths in recent years. These are telling examples of why stringent shutdown startup safety measures must be followed.
Buncefield Oil Depot explosion
A tank at the Hertfordshire Oil Storage Limited (HOSL) exploded on Saturday, Dec. 10, 2005, while being filled during the startup shutdown process. The tank’s eruption occurred despite two distinct forms of safety controls.
These involved a gauge that staff members could monitor while administering fuel. HOSL shutdown startup safety measures also included a separate independent high-level switch, referred to as an IHLS. This asset was designed to override human mistakes and stop the process if the tank was overfilled. In this case, the first gauge became stuck and the IHLS was not functioning correctly.
Control room team members received no advanced warning that excessive amounts of gasoline were flooding the tank. It eventually overflowed and created a massive vapor cloud that ignited. The fire lasted five days as first responders and firefighters worked to extinguish the fire and end the contamination.
A subsequent investigation into the SU/SD-related disaster revealed design and maintenance failures. Both primary monitoring assets, as well as the fuel containment failsafe system, had technical faults that led to the explosion. Officials also noted that human error and the following inadequate shutdown startup safety measures were root causes.
- Although independently audited, the SU/SD management systems in place at HOSL were flawed and staff members failed to follow safety protocols.
- Staff pressure had risen leading up to the explosion, and control room operators did not receive adequate intelligence to avert the catastrophe. The facility had ramped up production without necessarily onboarding experienced personnel, including engineering support.
BP Texas City Refinery Explosion
In March 2005, the BP Texas City refinery suffered an explosion after an isomerization unit (ISOM) was restarted following routine maintenance. Oversights, miscommunication, technical glitches, and a broad failure to follow refinery shutdown startup safety measures resulted in a staggering amount of flammable liquid hydrocarbons flooding a tower.
Technological and mechanical failures in early warning systems produced faulty data. As a result, safety professionals did not have access to accurate data showing that the flammable liquids had overwhelmed the tower. Although the tower was designed to take on less than 10 feet of combustible liquid, it ran to the top of the 170-foot tower.
Internal pressure rose to a critical 64 psi. After inadequate pressure relief valves were opened, the tower erupted. As the hydrocarbons splattered the area, a vapor cloud formed and spread across the facility. An idling pickup truck sucked in the fumes, backfired, and the explosion killed and injured on-site workers. More than 43,000 Texas City residents were urged to shelter in place within a three-quarter-mile radius.
A Chemical Safety Board probe uncovered the following.
- An ISOM procedure was in place to send excess liquid to a storage container. The valve was closed by a plant technician, and the tower took on three hours of unchecked fuel. None of the excess fuel was removed before startup steps began.
- A blowdown drum lacked the capacity to handle the massive overfilling even though a pressure relief valve appeared to be functioning properly. The company reportedly did not replace the blowdown drums despite prior safety warnings.
- Shift supervisors did not follow shutdown startup safety measures, tasking them with removing non-essential personnel from risk areas.
Phillips 66 Wood River Refinery
In February 2019, a fire injured workers when a distilling unit caught fire during startup. Following a planned maintenance shutdown, hydrocarbons were incorrectly funneled to a heat exchanger. Plant operators opened the wrong valve, allowing 50,000 pounds of flammable liquid to be released in approximately 8 minutes. The plant fire lasted nearly an hour.
Fire During Startup at Kuraray America
In May 2018, a facility in Pasadena, Texas, experienced a fire during startup preparations. The Kuraray America EVAL plant’s chemical reactor released more than 2,000 pounds of ethylene due to abnormally high pressure. The vapor ignited with more than 250 people on site. Twenty-one workers were reportedly injured and transported to an area hospital for treatment.
These examples illustrate the importance of proper planning, safety measures, risk assessment, and meticulous execution during SU/SD activities. Following strict safety protocols, conducting thorough inspections, and implementing effective maintenance practices are crucial to prevent such failures and their devastating consequences.
Reliability Programs Decrease Risk
The importance of reliability programs cannot be understated. They help support incident reduction by curtailing safety failure rates. These reliability programs can help mitigate SU/SD risks.
- Equipment Stability: Reliability programs can focus on preventative maintenance, replacement parts, inspections, and monitoring to minimize breakdowns.
- Safety Culture: It’s essential to create a culture of safety that empowers workers to tap the brakes and review issues during the startup and shutdown process. Supervisors must be free of corporate pressure to get systems back online safely, not quickly.
- Competency Training: Human error continues to plague wide-reaching industries. When people make mistakes or fail to communicate in plants and refineries, lives are at stake. Adhering to SU/SD safety measures and identifying vulnerabilities requires ongoing training.
A well-trained workforce uses job-specific PPE and has access to disposable personal protective equipment. International Enviroguard manufactures and distributes a complete line of disposable protective clothing and accessories that exceed industry standards.