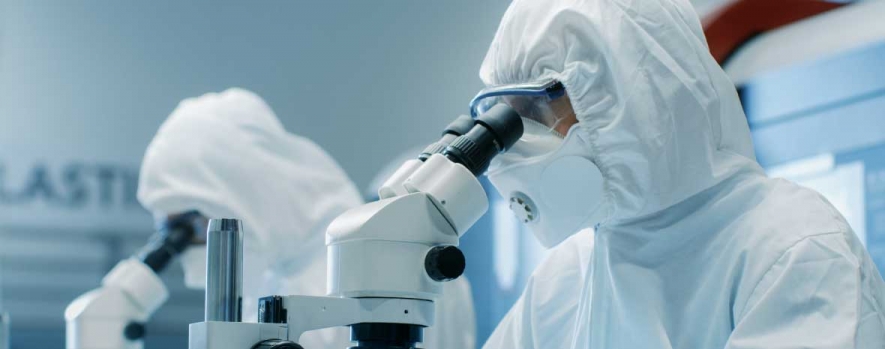
Industries concerned with high-level contamination defenses face a workspace challenge of reducing or eliminating airborne particles, vapors, and dust. Part of the process includes understanding the differences of controlled environment vs clean room and creating a strategy that ensures the best standard possible. Beyond the cleanliness protections that are physically installed, defending against personnel inadvertently contaminating a space calls for determined protocols and the use of personal protective equipment (PPE).
What is a Controlled Environment?
Sometimes referred to as a “critical environment,” a controlled environment is a defined space that sets parameters to regulate factors such as temperature, air pressure, humidity, dust, and separates designated personnel from others in a facility. Companies that employ controlled environment strategies limit human traffic and require some degree of personal protective clothing in the area.
Operations that implement controlled environment practices are not necessarily required to measure and regulate airborne particles. But specialized HVAC filters are usually monitored and replaced at a higher rate than many other industries. Concerns about controlling agents that are carried into the space by workers and visitors are routinely addressed. When comparing the controlled environment vs clean room standards, the latter imposes compliance standards in terms of contamination.
What is a Clean Room Environment?
Popular culture movies and binge-watching shows have widely generated the image of a clean room. Viewers see tight, enclosed spaces where researchers work in glistening white rooms. In pandemic films, minimalistic field research facilities are set up with flexible materials. The idea that a clean room tends to small is a common misconception. For example, semiconductor and solar panel manufacturing clean room spaces tend to be vast. In reality, entire plants can be immersed in practices that meet compliance standards.
Industry leaders are tasked with identifying and controlling the number of particles per cubic meter to meet International Organization for Standardization (ISO) thresholds. Decision-makers typically need to identify the appropriate level of sanitization and control the space to meet or exceed clean room ISO guidelines. It’s essential to understand that a clean room ranks among the various types of controlled environments. Sectors that leverage clean rooms include the following.
- Semiconductor Manufacturing
- Pharmaceutical & Biotech Industry
- Medical Device Manufacturing
- Life Sciences & Research
- Military Defense Contractors
- Aerospace
The important takeaways is that clean rooms are not defined by size, but rather by successfully regulating the enclosed environment. Like other types of controlled environments, clean rooms address temperature, humidity, airborne particles, and potential contaminants. Almost always, employee separations are imposed, and disposable protective clothing worn.
Who Has Access To A Clean Room?
Clean room personnel typically comprise a small group who have undergone contamination control awareness and training. At the highest level of clean rooms, limited groups may exit and enter through airlocked sub-rooms and undergo decontamination procedures.
Before entering, personnel typically decontaminate and then put on protective wear such as lab coats, face masks, hairnets, gloves, foot coverings, and full protective coveralls, among others. In stringent clean room workplaces, people may undergo decontamination to eliminate releasing a biohazard into the general public when exiting as well. Protective garments are disposed of in a secure exit room, driven by regulatory oversight.
Clean rooms usually earn their classification based on how few airborne particles are present per cubic meter. Although the ISO scale enjoys international acceptance, countries often have unique regulations and compliance standards.
How To Maintain A Clean Room Environment
Clean rooms spaces are routinely set up as standalone, portable spaces within controlled environments, as well as full facilities. They usually achieve clean room classification be using specialized infrastructure, such as the following.
- Airflow devices employ a series to finer filters to minimize dust
- Specialized lighting fixtures
- Specialized containment walls and plastics
- Air filtration systems
- Temperature & humidity controls
- Ironizing materials to control static electricity
- Airlocks & decontamination spaces
- Disposable PPE
A need for well-regulated clean rooms appears to be growing in conjunction with technological advancements. Electronic devices now include miniature parts and wiring that must be free of dust particles and condensation. This factor has given rise to more manufacturing facilities upgrading to clean room standards.
In many ways, next-generation technology manufacturers must regulate their workspace in terms of environmental cleanliness. Despite living in a quickly evolving technology age, everyday people pose the highest risk to a secure clean room.
PPE Necessary To Maintain Controlled Environments & Clean Rooms
Industry leaders can design a controlled environment or a more stringent clean room with technology and products that insulate it from airborne particle breaches. But the X-factor is that individuals will enter and exit this space, carry potential contaminants on the clothing, skin, and hair. At no fault of their own, your valued team members represent the greatest risk to a clean room. According to reported Austin Index statistics, these are ways workers can generate particle contamination.
- Workers no in motion generate at least 100,000 particles/minute 0.3 microns
- Shifting one’s position causes upwards of 2,500,000 particles/minute, 0.3 microns
- Walking generates at t 5,000,000-7,500,000 particles/minute, 0.3 microns
- Negotiating a flight of stairs generates approximately 10,000,000 particles/minute, 0.3 microns
These statistics support the ongoing use of clean room PPE to eliminate contamination. Responding to the industry needs to control particle infestations, International Enviroguard provides clean room PPE that ensure sanitization controls. These include the following.
- ChemSplash: This product line has emerged as a go-to lab coat protection widely used in controlled environments. It minimizes airborne particles while protecting workers against hazardous materials.
- Body Filter: This breathable coverall comfortably insulates clean room personnel by delivering up to 99 percent micron protection, on par with an N95 respirator. This PPE line also includes a product with a fixed hood.
- ViroGaurd: Designed with bloodborne pathogens in mind, the head-to-toe protection delivered by this top-tier PPE exceeds industry standards for particle transfer containment.
- PPE Accessories: PPE better reduces potential controlled environment contamination when used in conjunction with accessories such as non-skid shoe coverings, 3-ply pleated face masks, hair coverings, and gloves, among others.
Wide-ranging industries are likely to see an increased need to establish clean room standards for manufacturing, testing, and research. While physical infrastructure and maintenance are foundational compliance elements, only PPE can eliminate personnel contamination breaches. International Enviroguard produces industry-leading controlled environment PPE products.