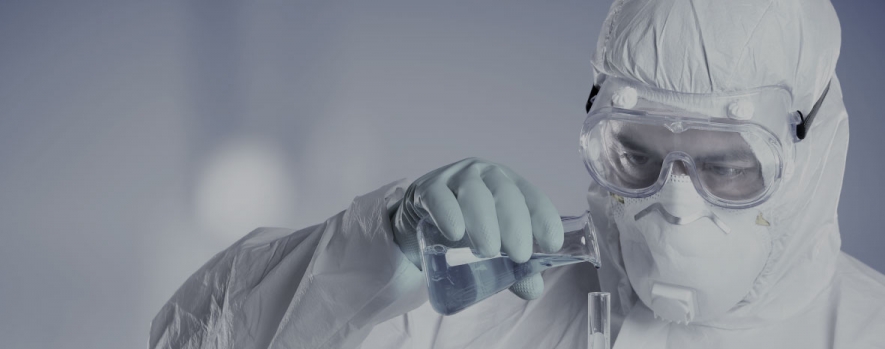
The intent of a cleanroom is to strictly monitor and control the concentration of airborne pollutants—such as microbes, aerosol particles, chemical vapors, and dust—that are present in the air. To accomplish this high degree of regulation, cleanroom equipment typically includes filters, air pressure controls, air locks, and several other design elements.
For successful contamination prevention, employees who work within cleanrooms must also wear appropriate protective apparel.
Understanding Cleanroom Classifications
Cleanrooms vary in complexity and size, depending on need. Currently, there are nine cleanroom classifications as outlined by the International Standards Organization, known collectively as ISO 14644-1 Standards. These standards are adopted from the now-defunct United States Federal Standard 209E, which was officially canceled by the General Services Administration of the US Department of Commerce in November of 2001 (although the US FED Standard 209E is still widely used among various industries).
The ISO 14644-1 Standards are divided into classifications known as ISO 1 through 9. Effectively, these delineate varying degrees of air cleanliness. To meet requirements of a cleanroom, the air within an enclosed space must not exceed a particulate count as detailed by that room's specific ISO classification. Most cleanrooms must be tested on a routine basis (ideally by an independent agency) to ensure that the classification specifications are met. Cleanroom monitors are also valuable design elements which help to assess the cleanliness of the air on a real-time, day-to-day basis.
As a reference, ambient room air contains approximately 35,200,000 particles per cubic meter measuring at 0.5 micron and larger. This is equivalent to an ISO 9 cleanroom classification, which is the lowest level of cleanroom standards.
Conversely, an ISO 1 cleanroom classification must contain no more than 0.35 particles per cubic meter at 0.5 micron and larger. And an ISO 5 cleanroom classification (which is equivalent to class 100 from the retired-US FED Standard 209E) must contain no more than 3,520 particles per cubic meter measuring greater than or equal to 0.5 micron.
The fact that cleanrooms can be designed so stringently and effectively is nothing short of impressive. One micron is one-hundredth the width of a single human hair—but many cleanrooms can regulate particles as small as 0.01 to 0.05 microns in width.
Additionally, consider the amount of airborne particles the typical human body is poised to introduce to an environment: a person sheds dead skin cells (in the form of microscopic skin flakes) at a rate of about 1 billion flakes per day, and the typical flake of skin is about 35 microns in diameter. As a result, protective apparel is a critical element to preserving the integrity of the cleanroom environment and the people and products within these environments.
Selecting the Right Protective Apparel for Cleanrooms
Protective attire worn by cleanroom employees must be able to minimize the amount of flakes, microbes, and hair from an employee's body which gets into the air, while at the same time preventing external particles from coming in contact with an employee's body.
Additionally, protective apparel must be sufficiently breathable and functional to allow staff to perform their duties without running the risk overheating or becoming distracted by physical discomfort.
In the same way that cleanroom classifications specify the number and size of particles present per cubic meter of air, these classifications may also dictate which type of PPE is necessary for the employees working within them. Common PPE used in cleanroom environments include shoes, boots, shoe and boot covers, hairnets, beard covers, coveralls, face masks, frocks and lab coats, gowns, aprons, gloves, sleeves, and bouffant caps. These garments must be made with durable material that will withstand the length of time spent and type of tasks performed within a cleanroom.
The advantage of disposable cleanroom PPE in particular is the decreased risk of contamination from within and without the enclosed space. Most cleanroom set-ups provide specific areas where employees can doff and safely dispose of their attire, preventing any microbes and particles from leaving the enclosed space and entering the community-at-large.
In addition to wearing the appropriate protective garb, all personnel engaging with cleanroom environments must be trained in correct contamination control theory. Depending on the specific cleanroom within a given industry or company, protocols often include specific ways to don and doff PPE as well as specific methods for entering and exiting the enclosed space.
International Enviroguard Cleanroom PPE Options
International Enviroguard proudly offers a range of disposable PPE acceptable for cleanroom classifications ISO 5 through 9, including:
- GammaGuard® CE: experience unparalleled sterility assurance levels and tear- resistant, low lint garments that will further reduce the risk of contamination. Our GammaGuard® CE is sterilized to 10-6 for superior sterility assurance. Sterile Don™ packaging assures the wearer can don the garment with less contamination risk.
- MicroGuard CE®: for cleanroom environments without a sterile requirement, our MicroGuard CE® provides effective barrier protection from liquids and particulate matter. With strong bound seams, the risk of particulate generation is decreased, and the suits' innovative design allow for maximum comfort and functionality.
Do you have employees working in cleanroom environments? Ensure your personnel and your products are protected by utilizing the appropriate protective apparel to suit the environment. To learn more about your options and procure the right protective apparel for your company, contact International Enviroguard today. Our products are manufactured in ISO-certified facilities