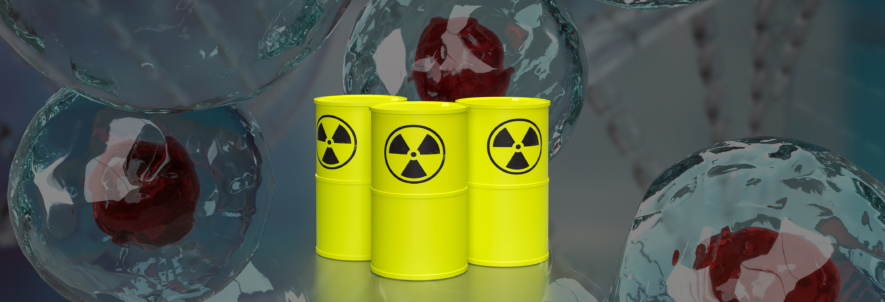
The advanced technology recycling industry continues its rise, enjoying a market value expected to approach $600 million by year’s end. That figure hovers at nearly four times its global value in 2021, and experts predict the sector will exceed $6 billion in 2031.
The U.S. is home to about 11 such facilities, and Big Oil has entered the market by creating mega-facilities in recent years. ExxonMobil built a massive petrochemical refinery complex in Baytown, Texas. The multinational corporation reportedly plans to build chemical recycling plants alongside many of its manufacturing locations. Although resources have not yet been committed to these projects, Louisiana, Illinois, Belgium, and Singapore locations appear to be in play.
While the benefits of chemical plastic recycling have been touted, plants may also bring a health and safety downside. Stringent chemical plastic recycling safety measures and consistent use of personal protective equipment (PPE) and disposable clothing are vital to protect the health and safety of chemical recycling plant workers.
What is a Chemical Recycling Plant and What Does it Do?
At a fundamental level, chemical recycling technologies use heat and chemicals to reduce plastic waste into raw materials for the purpose of making new products, fuel, fertilizer, and other chemicals.
It’s essential to understand that plastics are made from oil and petroleum produced by companies such as ExxonMobil. Manufacturers employ a polymerization process that involves combining long chains of molecules. Final plastic products vary in size, shape, color, and recyclability.
The global output of plastics runs upwards of 380 million tons, and only specific single-polymer plastics are typically recycled. In Europe, approximately 15 percent of plastic products are repurposed, and the U.S. manages to reconstitute only about 9 percent. The vast majority end up filling landfills and oceans or littering the environment.
Chemical plastic recycling brings a game-changing process to the equation. Plastics are recycled by breaking them down into molecular parts. The process sanitizes the materials and converts them back into raw materials, known as petrochemical feedstock. The feedstock can be used to produce new products, reducing landfill accumulations and litter. These are the three processes used in chemical recycling.
- Dissolution: This part of the process immerses the polymers in solutions that eliminate additives. The dissolved plastic breaks down to its initial polymer status.
- Depolymerization: Employing chemicals and heat reduces the size of polymers into molecules known as “monomers.” The monomers are then used as secondary raw materials in plastic production.
- Conversion: This process utilizes chemicals, high temperatures, and catalytic processes to break down plastic products into gaseous (gasification) or oily feedstock (pyrolysis) in a reactor.
Advanced technology recycling facilities generally use either thermal crack or gasification to complete the conversion process. Both are conducted in a low-oxygen environment and intense heat to recreate usable materials for plastic products, fertilizer, or fuel.
Benefits of Chemical Plastic Recycling
One of the core benefits of chemical plastic recycling involves reducing landfill waste and littering. The U.S. Government Accountability Office released a report in 2021 indicating the country sends more than 75 percent of all plastic materials to landfills.
Tallying nearly 30 million tons in landfills, upwards of 199 million tons currently float on ocean surfaces. Some estimate that 1.8 trillion plastic items pollute the oceans, covering an area twice the size of Texas.
According to ExxonMobil, its mega-facility in Texas can recycle more than 80 tons of plastic yearly. The oil giant reportedly has plans to expand its overall capacity to 1 billion pounds per day by 2027. ExxonMobil would recycle upwards of 26 million tons of plastic annually at that rate.
As other major corporations, such as Dow, Eastman, LyondellBasell, PureCycle, and Cyclyx, jump into the chemical recycling sector, the advanced technology used can reduce plastic pollution on land and sea. These are other benefits of chemical plastic recycling.
- Hard-to-Recycle Plastics: Not all plastics are created equal, and some cannot be broken down into usable raw materials through traditional processes. The advanced technologies that drive chemical recycling expand the types of plastics that can be repurposed. Without this option, reducing waste and pollution would likely go unchecked.
- Reduce Air Pollution: Often referred to as “greenwashing” because incineration eliminates physical products, reports indicate that plastic burning continues in the U.S. and ranks among the primary ways some countries handle waste. Environmental advocacy groups suggest that in the U.S. and other countries, the amount of plastic burned exceeds recycling. Plastic incineration releases hazardous agents that include lead, mercury, nitrogen oxides, sulfur dioxide, volatile organic chemicals (VOCs), and microplastics, among others.
- Virgin Materials: Unlike other recycling options, chemical processes restore the used materials to their original composition, often called “virgin.” This allows companies to recreate products that require higher-quality materials.
The U.S. and other nations have implemented bold policies to address carbon emissions. From electric vehicles to harnessing renewable energy resources, lawmakers and environmental advocates are determined to improve air quality and end negative impacts on the planet. One of the crucial benefits of chemical plastic recycling involves reducing fossil fuel emissions. Some experts point to these advanced technological facilities reducing greenhouse gases by 19-48 percent compared to older plants.
Recycling also allows companies to convert plastic waste into fuel without engaging in the complete production process. Reproducing plastic products requires only a fraction of the effort and emissions used to make items initially.
Chemical Plastic Recycling Safety Measures
Driven largely by profitability, major corporations are poised to invest hundreds of millions because chemical recycling plants improve their bottom lines. It’s safe to say that many of the same safety issues found in older plants exist in new chemical recycling facilities.
Adding intense heat of more than 1,000 degrees Fahrenheit and a variety of chemicals to break down plastics create an even more dangerous landscape. These are health and safety risks employees encounter in recycling plants.
- Chemical Exposure: Methanol, ammonia, hydrocarbons, and acetic acid are commonly used in plastic recycling. Exposure to ammonia fumes alone can burn the eyes, nose, throat, and respiratory tract. Skin contact with these and other agents can result in redness, swelling, sores, and poisoning.
- Airborne Particles:Flaking and chipped items can become airborne, causing lung damage and illnesses when inhaled. The recycling process also reduces items to small molecules that can go airborne. Breathing in unnatural elements has a negative effect on human health and well-being.
- Spillage: The National Safety Council reports that hundreds of thousands of people suffer significant injuries from slips and falls. These hard impacts rank among the most prevalent reasons employees receive emergency medical care, suffer long-term conditions, and end up on workers’ compensation. Recycling plants are not immune from this health and safety problem.
- Moving Machinery: Even advanced plastic processing plants use machinery to move items. Conveyors and other equipment pose a danger to workers in terms of hard impacts and snagged clothing. Loose-fitting sleeves, coveralls, and pant legs can become entangled and pull hard-working staff members into moving machinery.
Used plastic bottles, containers, and other items do not necessarily arrive sterilized at recycling facilities. Bacteria and other contaminants pose a grave danger to workers’ health. That’s why chemical plastic recycling safety measures rely on PPE and disposable clothing to ensure people finish their shifts without incident or injury.
What PPE is Needed at Chemical Recycling Plants?
Workplace safety requires employees to follow best practices and guidelines to avoid injuries such as slips and falls. Establishing protocols such as cordoning off wet floors and areas where chemical spills occur is one way companies can protect everyday people. Plants should also always have a spill kit on hand to safely clean any chemical spills. Maintaining an inventory of the following PPE and disposable clothing remains critical.
- Hard Hats and high-traction footwear, like rubber/PVC boots
- Chemical-resistant coveralls and/or chemical-resistant accessories (sleeves, aprons, etc.)
- Goggles and face shields
- Foot coverings and gloves
- Breathable masks and respirators
It’s also prudent to provide workers with a designated area to don and doff PPE, properly fitting disposable clothing, and a clean dressing area. Otherwise, chemicals and biohazards can be transferred, finding their way into the homes of recycling plant workers.