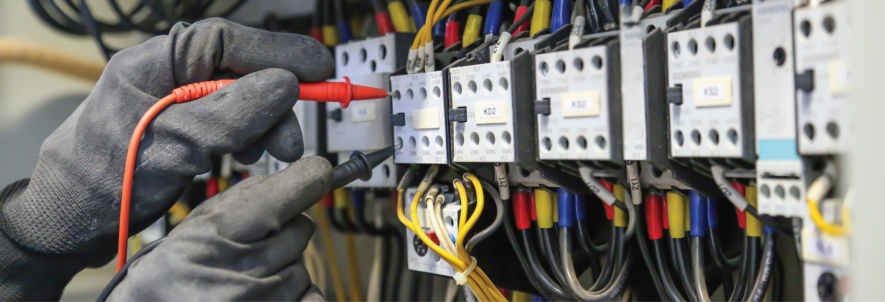
Living in the modern age means that we rely heavily on electricity. Electric power is vital for everything from computers and servers to lights and printers. Job sites rely on electricity to run heavy machinery and power various operational systems. However, while electricity is so valuable, it's also dangerous. When workers are exposed to hazardous electric sources, they can get seriously injured and even die.
Because of the dangers involved, it's imperative to understand how to keep employees safe at all times. So, we're going to look at the top safety tips for working with electrical wires and what you can do to maintain a safe and healthy workplace.
A Primer on Electrical Wire Injuries and Incidents
To help illustrate why electrical wires are so hazardous, let's look at some numbers. The Electrical Safety Foundation International helps monitor and track injuries and deaths caused by electrical hazards on the job.
- In 2019, 166 workers died from electrical incidents. That number was the highest in eight years, with a previous high of 174 workers in 2011. The lowest death count in the intervening years was 134 in 2015. The rise and fall of workplace deaths illustrate the need for constant vigilance and protection. When employers and employees get complacent, bad things can happen.
- The most dangerous industry for electrical deaths is construction, which accounted for 43 percent of fatalities in 2019. In second place is the utility industry.
- Oddly enough, while 2019 was the deadliest year for electrical accidents, it also had a relatively low number of injuries (1,900) compared to previous years. Ironically, 2015 saw the highest injury count with over 2,400 - the most within the same eight-year span.
- In 2019, there were over 110,000 structural fires in non-residential buildings. Of those, around eight percent of them were caused by electrical malfunction (8,095 total).
As you can see, electrical hazards can cause significant losses, both in lives and property damage.
What OSHA Says About Electrical Wire Safety
The Occupational Health and Safety Administration is responsible for setting safety guidelines for workers handling electrical wires. There are a few specific codes that address the issue, so let's break them down.
OSHA Electrical Safety Standard 1910.137(b)(2)
Code 1910.137(b)(2) refers to the type of personal protective equipment that employees should wear at all times. Employers are responsible for providing this PPE and training all workers on how to use it properly. Failure to do so can result in steep fines, not to mention injuries and potential deaths on the job.
As a rule, OSHA requires:
- Rubber gloves
- Face shields
- Safety shoes or boots
- Insulating sleeves
- Flame-resistant clothing
Depending on the type of work being done, employees may need additional PPE for extra protection. For example, if a worker is handling hazardous chemicals, they may need a respirator or breathing apparatus to ensure that they don't inhale toxic fumes. Regardless of the job, employers still have to provide sufficient PPE for all employees.
In addition to PPE, OSHA provides guidelines for insulating protective equipment (IPE). Workers will use IPE to help facilitate their tasks, but IPE is not worn like PPE. Some examples of IPE include
- Insulating line hoses and hoods
- Insulating barriers
- Live-line tools like shotgun sticks or hotsticks
Employers must test both PPE and IPE regularly to ensure that they can protect workers sufficiently. If items are used regularly, OSHA recommends testing gear about once a month. Employers must also provide formal examinations in between onsite testing. Gloves should be examined every six months and insulating sleeves every year.
OSHA Electrical Safety Standard 1926.431
This standard relates to equipment upkeep and maintenance. If employers don't inspect, repair, and upgrade their machinery, that can lead to failure and electrical injury or death. This specific standard refers to the construction industry, but the recommendations work well for all job sites. Some elements of standard 1926.431 include:
- Explosion-Proofing- Employers must maintain equipment so that there is little to no risk of an explosion due to electrical malfunction.
- Dust Proofing- Dust can get into machinery and cause various problems, both mechanical and electrical. Employers must protect all gear from dust-related incidents that could lead to an explosion or electrical arc.
- General Maintenance and Upkeep- Employers and employees must monitor equipment and machinery to watch out for loose screws, gaskets, and other pieces that may interfere with dust and explosion prevention.
- Reporting and Repair- If a worker spots any issues with machinery, they have to report to a supervisor immediately. Once a report is filed, the employer must stop using the circuit until the problem is fixed.
OSHA Electrical Safety Standard 1926.416(a)(3)
As we'll discuss in the next section regarding electrical safety precautions, workers need to know where circuits are at all times and how to shut them off. Typically, the best way to avoid electrical injuries or fatalities is to stop the flow of power from the source.This standard outlines various requirements for employers, such as labeling circuits with easy-to-spot signage, warning employees before they start work in an area with a live circuit, and locating and inspecting circuits regularly.
8 General Safety Tips for Working with Electrical Wires
Before your employees start working with or around electrical wires, they should be trained in proper safety techniques and precautions. Here are some generalized tips that can help prevent a disaster.
1. Make a Plan
The best way to avoid harm is to draft a project plan beforehand. During the planning phase, workers can assess the equipment and environment to spot any potential hazards. Planning can ensure that workers will use the proper PPE and IPE during the job and that they'll know where the correct circuit is for shutting off power.
2. Wear the Right Clothing and Gear
As we mentioned, OSHA requirements say that workers should have rubber gloves, insulating sleeves, and safety glasses on at all times. Fire-resistant clothing can also help prevent injury because the fibers are not very conductive or are treated with a flame-retardant. During the planning stage, employers and employees can determine whether additional PPE is necessary. Workers should also avoid wearing any metal, such as watches or jewelry.
3. Use the Buddy System
Should the worst happen, your workers shouldn't be by themselves on the job. A buddy system helps ensure that someone can always call for help if necessary or perform CPR. Both individuals should be trained in electrical safety and CPR before starting work.
4. Use the Lock Out Tag Out (LOTO) System
There are six steps to the LOTO system, and they can help ensure that all circuits are shut off and de-energized before working. De-energizing a circuit simply means making sure that there is no residual power left in the wires or machinery.
- Step One: Inspect the System- Before starting work, employees should be able to assess hazards on the fly, even if they didn't come up during the planning phase.
- Step Two: Shut Down the Circuit- Workers should know how to power down the circuit entirely so that there is no low-level residual energy.
- Step Three: Isolate the Equipment- Shut off any valves, unplug any cords, and separate the machinery from all electrical sources.
- Step Four: Lock and Tag- Any switches or buttons that can turn the equipment on should be locked in the off position. Doing this ensures that no one can accidentally activate the system. Each lock should have a corresponding tag with the worker's name and contact information.
- Step Five: Check for Stored Energy- Depending on the equipment, workers should be able to test for any residual electricity within the system. If they detect anything, they should also be able to discharge any stored energy.
- Step Six: Verify Everything- Employees should double-check and walk through all previous steps again to ensure that they didn't miss anything.
5. Avoid Working in Wet Areas
Since water is such a potent electrical conductor, it can pose significant safety risks on a job site. Even damp areas can be a problem, so workers must be able to address it. For example, if there is standing water on the ground, employees can either dry it off or cover it with non-conductive material (i.e., a wooden board).
6. Use a Ground Fault Circuit Interrupter (GFCI)
GFCIs are portable devices that workers can plug into an outlet or circuit. If there is a power surge because someone is getting electrocuted, the GFCI will detect it and kill the power automatically. Using these devices can act as a final failsafe just in case something else goes wrong.
7. Stay Away from Overhead Power Lines
OSHA recommends a minimum safe distance of 10 feet from any overhead electrical wires. Many injuries and accidents happen because of overhead lines, so workers should be hyper-aware of them.
8. Inspect Power Cords and Outlets for Damage
Finally, workers should check all electrical wires and elements, including plugs and outlets. Any damaged components should get replaced immediately. For example, if a three-pronged plug is missing the grounding prong, employees should swap it out with a new plug. They should look for signs of burning or charring, as that can indicate exposed wiring and potential electrical sparks.
Get Your Safety Gear from International Enviroguard!
Electrical safety is crucial for any workplace, particularly those where heavy machinery is involved. International Enviroguard can help keep your employees safe by providing high-quality, OSHA-ready personal protective equipment.