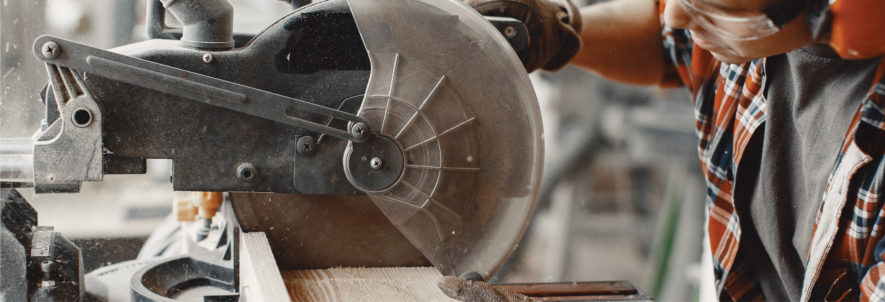
Accident prevention in the workplace tasks companies with adopting policies to ensure employees complete their shift safely. Despite evidence that construction sites, manufacturing plants, fabrication facilities, and others using heavy machinery sustain upwards of 340 million injuries annually, regulations such as OSHA machine guarding requirements are not always followed.
According to the International Labor Organization, 2.3 million workers suffer work-related illnesses or accidents annually. That’s why corporations that require workers who operate or perform tasks around dangerous equipment to implement meaningful safety procedures that increase human safety. Industry leaders often discover the same tips for machine maintenance, and mandating personal protective equipment also support accident prevention in the workplace.
1. Schedule Routine Machinery Maintenance
Companies that wait to perform maintenance until machinery fails or falters cause additional issues. Reactive maintenance negatively impacts an organization’s bottom line because it disrupts productivity or causes shutdowns until machinery is back up and running at peak performance. Along with pushing equipment to its breaking point, generally reactive maintenance creates a climate in which an apparatus continuously underperforms.
The cost of calling in technicians or ordering parts — which can result in supply chain delays — only worsens an already bad situation. Experts determine the cost of reactive maintenance to be 2-5 times more expensive than proactive policies. Along the way, the decreased or less than maximum performance of workplace tools becomes increasingly hazardous.
Corporate leaders who do not mandate regular machinery maintenance produce a workplace where valued employees are placed into harm’s way. Improving profits and sparing employees from unnecessary work-related injuries should be common sense.
2. Mandate On-the-Job Safety Training
A 2016 article published by Safety & Health magazine indicates that only 1 out of 5 workers in Toronto do not recall receiving safety training. The report also highlights that people are three times more likely to suffer a work-related injury during their first month.
Other revelations point to workers in the agriculture, forestry, and fishing industry suffering 45.4 percent of the injuries and illnesses in 2013, with construction and extraction involving 34.9 percent. The U.S. Bureau of Labor Statistics reports that private industry injuries totaled 2.7 million in 2020. And although that number declined from 2.8 million the previous year, some safety experts say new hires suffer upwards of 40 percent of workplace injuries.
These trends can be decreased by developing a safety regimen that requires new hires to undergo rigorous training before operating equipment. Best practices typically involve an educational component and oversight from an experienced professional. Not only will safety training reduce the likelihood of an inexperienced worker suffering an injury, but the process also teaches how to properly use the equipment. That means they are less likely to damage expensive tools or machinery.
3. Require that Electric Safety Protocols are Followed
Non-fatal workplace electrical injuries hit 2,220 in 2020, an increase of 17 percent from 2019. That represents a troubling and largely unnecessary trend, according to the Electrical Safety Foundation International (ESFI). The safety organization reports the following incurred more than two-thirds of all electrical injuries.
- 20 – 24 years old: 22 percent
- 25 – 34 years old: 24 percent
- 35 – 44 years old: 22 percent
The conventional wisdom regarding these work-related accidents often revolves around knowledge — or lack thereof — regarding electricity. But what may prove discouraging is that loose cables and frayed wiring result in contact electrocutions. Defective cables remain a persistent health and safety hazard.
That’s why part of a thoughtful routine maintenance plan must include wiring checks. Standard procedures usually revolve around the use of tubing or sleeves over cables that can be stepped on or sustain impact. However, safety leaders should also consider moisture and ways highly conductive water can be kept away from power sources.
4: Cleanup & Maintenance Minimize Falls, Damage & Airborne Particles
Organizations that make cleanliness a workplace value send a subtle message that the condition of the environment and equipment matters. A space free from debris also reduces the number of slips, trips, and hard impact falls. According to the Centers for Disease Control and Prevention, 27 percent of the 888,220 non-fatal work injuries in 2019 resulted in people taking time off and recovering. More than 2.4 million hard-impact falls resulted in employees requiring an emergency room visit. That’s why dealing with the following hazards is highly important:
- Damaged Walkways
- Wet or Dusty Floors
- Exposed Cables
- Debris Accumulating on Stairways
- Loose or Missing Handrails
Dust and debris also lead to severe workplace illnesses that include reduced lung function, as well as a wide range of internal organ issues. That’s a good reason for decision-makers to insist on everyone utilizing personal protective equipment such as a breathable mask. In terms of supervisors maintaining safe equipment, the same airborne particles also clog and damage machine components. Build up of dust and debris on machinery can damage it, make it less effective, or force it to work harder leading to overheating and other complications.
5: Prioritize Potential Loss of Limb Hazards
More than 185,000 people in the U.S. require limb amputation each year, according to the Amputee Coalition. More than 2.1 million are living without a limb, and that number is expected to climb to 3.6 by 2050, with 36 percent struggling with depression as a result. The Amputee Coalition indicates there are three top reasons why more than 500 people suffer these tragic losses daily.
- Vascular diseases such as diabetes and blood clots result in 54 percent of limb losses.
- Cancer patients require amputations at a rate of less than 2 percent.
- Traumatic accidents that include workplace injuries cost 45 percent of people a limb.
Statistics compiled by OSHA indicate 8,000 employees require an amputation each year, and 44 percent of the victims were involved in the manufacturing sector. The workplace safety organization issues guidelines to prevent severe injuries that result in loss of limbs. Its definitive publications, called “Safeguarding Equipment and Protecting Employees from Amputations,” tasks companies with recognizing potential hazards and deploying safeguard devices.
The guidance covers wide-reaching equipment that specifically reviews meat-cutting band saws, roll-bending machines, printing presses, conveyors, and shearing machines, among many others. One of the insightful ways companies can prevent tragic injuries such as amputations is to employ Lockout/Tagout protocols, also known as LOTO safety.
6: Implement OSHA’s LOTO Safety Strategy
The LOTO safety standard 29 CFR 1910.147 is designed to augment other machinery practices. When followed, hazardous objects and energy are more effectively controlled. Company safety leaders typically craft a set of procedures that ensure machinery has no power running to it when maintenance and repair are conducted. LOTO safety protocols prevent high voltage from making contact with technicians and prevent machinery from jolting or restarting unexpectedly.
Although specific to a facility’s equipment, workspace, and industry, they generally involve the following:
- Develop and train employees to follow a company-specific LOTO safety policy.
- Provide specific locks to prevent access to energy sources.
- Employ a recognized set of color-coded and labeled tags during lockouts.
- Ensure that new and modified equipment can be locked out.
- Provide step-by-step guidelines to safely restore power to machinery.
Other ways to make LOTO safety standards increasingly reliable include tasking only certified team members with implementation. Consider always having a supervisor oversee lockout and power restoration. Require safety teams to review the LOTO safety policies annually and make changes when necessary.
7: Require All Employees to Wear Appropriate PPE
The importance of personal protective disposable clothing and equipment cannot be understated. These layers of safety materials prevent harmful agents from making skin contact. High-quality products also stop airborne debris from entering the eyes, ears, or lungs. Having suitable PPE and clothing also enhances workplace safety for valued employees who manage machinery and commercial equipment in the following ways.
- Eye Protection: Protective eyewear stops airborne particles, debris, and chemical splatter from temporarily or permanently blinding workers. When operating hazardous equipment, an impaired person can easily lose control of machinery.
- Breathable Masks: Disposable breathable masks are quickly becoming the standard in wide-reaching sectors. These inexpensive PPE items prevent the spread of germs while stopping crystalline silica particles, wood dust, and more from entering the lungs.
- Headgear: Hard hats minimize the impact that might otherwise result in a traumatic brain injury. In spaces that may not present hard-impact risks, hoods and one-piece coveralls prevent dust settling on a person’s head. Headwear can also prevent hair from getting snagged in moving parts.
- Coveralls: Mandating coveralls ranks among the best ways to prevent hazardous materials from making skin contact with employees. But when utilizing commercial tools and machinery with moving parts, it’s essential to select appropriately fitting PPE and disposable clothing. Loose sleeves and poorly designed protective clothing can get caught, resulting in a significant injury or loss of limb.
Organizations determined to make accident prevention in the workplace a centerpiece of their standards are best served by having a complete inventory of personal protective clothing and equipment on hand. It’s essential the products allow free movement while reducing the risk of sleeves or leg coverings getting caught machinery. International Enviroguard produces a complete line of certified protective wear that maximizes safety in the workplace and exceeds safety standards.